July 2024 - Fuel pump
I backed out of our driveway one day and thought I’d stalled the car from not giving it enough revs, but then the car didn’t want to start back up. I could hear the main fuel pump running so figured it might be spark or ECU or something else..
I was stuck diagonally across my road, and with the help of a neighbour and the starter motor, I got it off the road and back into the driveway.
I tested injector firing to rule out CPS, ECU and injectors and tested a timing light on the spark leads, so my eyes turned to the fuel system.
I'd read on a turbobricks thread that a failing lift pump can sometimes cause this issue, particularly when it's just under half a tank (which it was) so started looking at that.
I tested the fuel pumps individually and both seemed to be working from what I could hear, and with no further diagnosis I consulted fellow 940 enthusiast @nugget_940 for advice after coming across his thread on the topic.
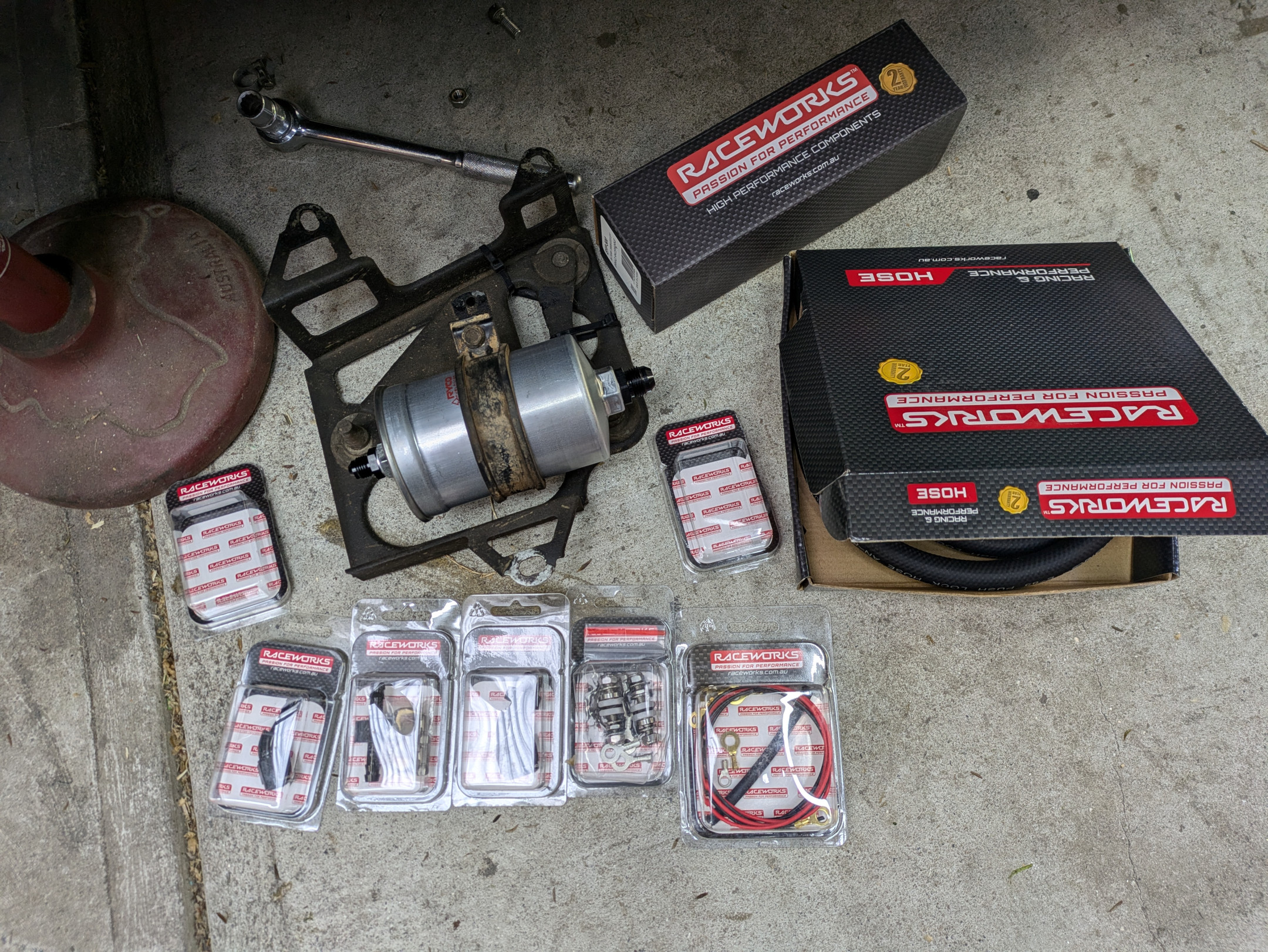
After some rather exuberant spreadsheeting in collaboration with him regarding parts required, I fired up the parts cannon and taking advantage of EOFY sales, got some shiny new parts for the fuel system, specifically:
Raceworks EFP-500 340lph E85-compat fuel pump
New E85 compatble hoses (5/16” and 1/2”) - (HPH-080-05M, RWH-400-08-1M)
New stock Ryco fuel filter (Z311)
Wiring bulkheads (FSA-499)
Fuel-safe heatshrink, wiring and fuel hose (FSA-095)
Fittings for fuel filter (RWF-731-06BK, RWF-732-08BK)
Barbs for fuel filter fittings (RWF-402-08BK, RWF-412-06-05BK)
Submersible 8mm hose - (Dayco 80160)
With everything in hand, I started pulling the old stuff out and got a bit of a surprise.
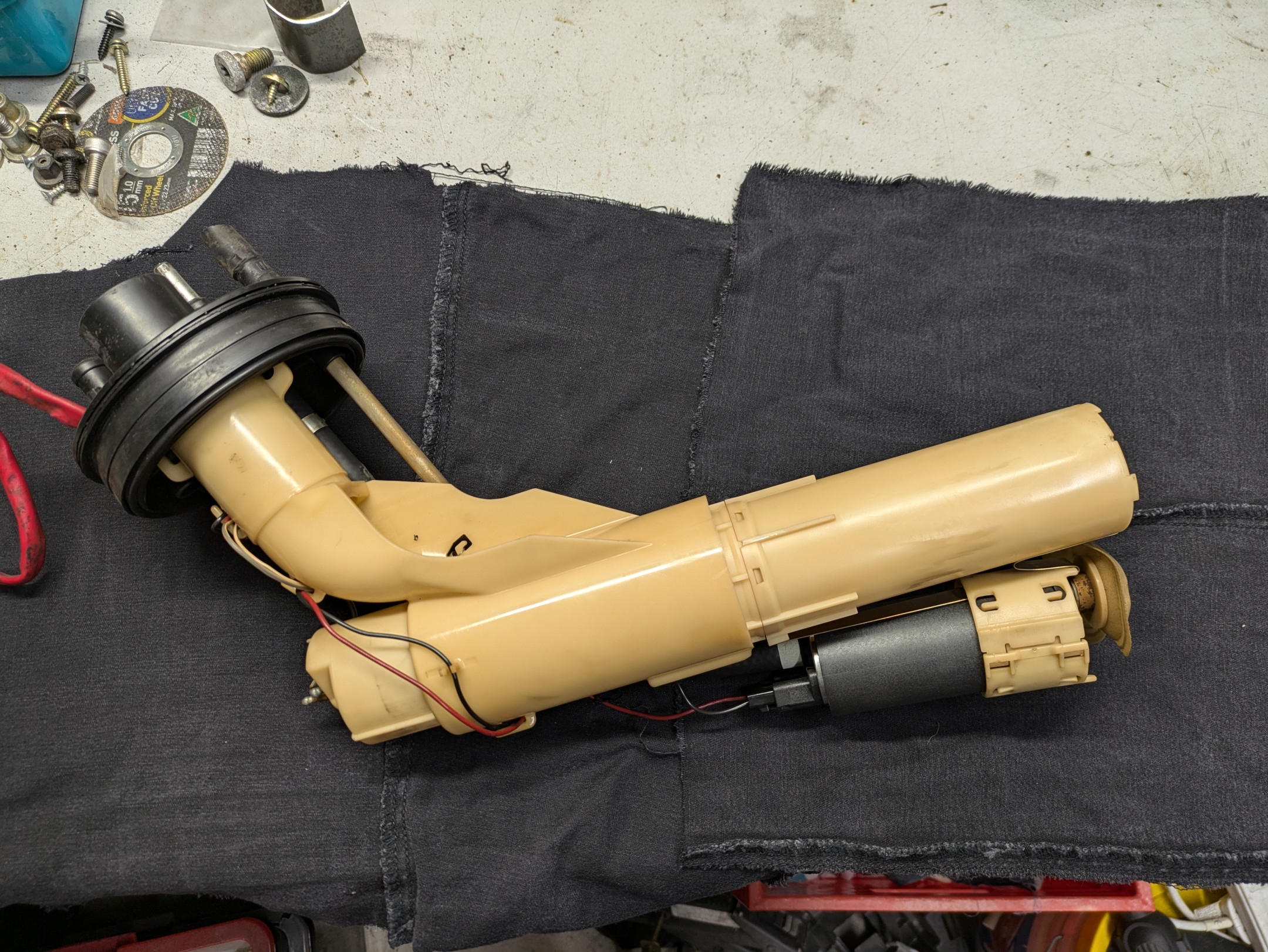
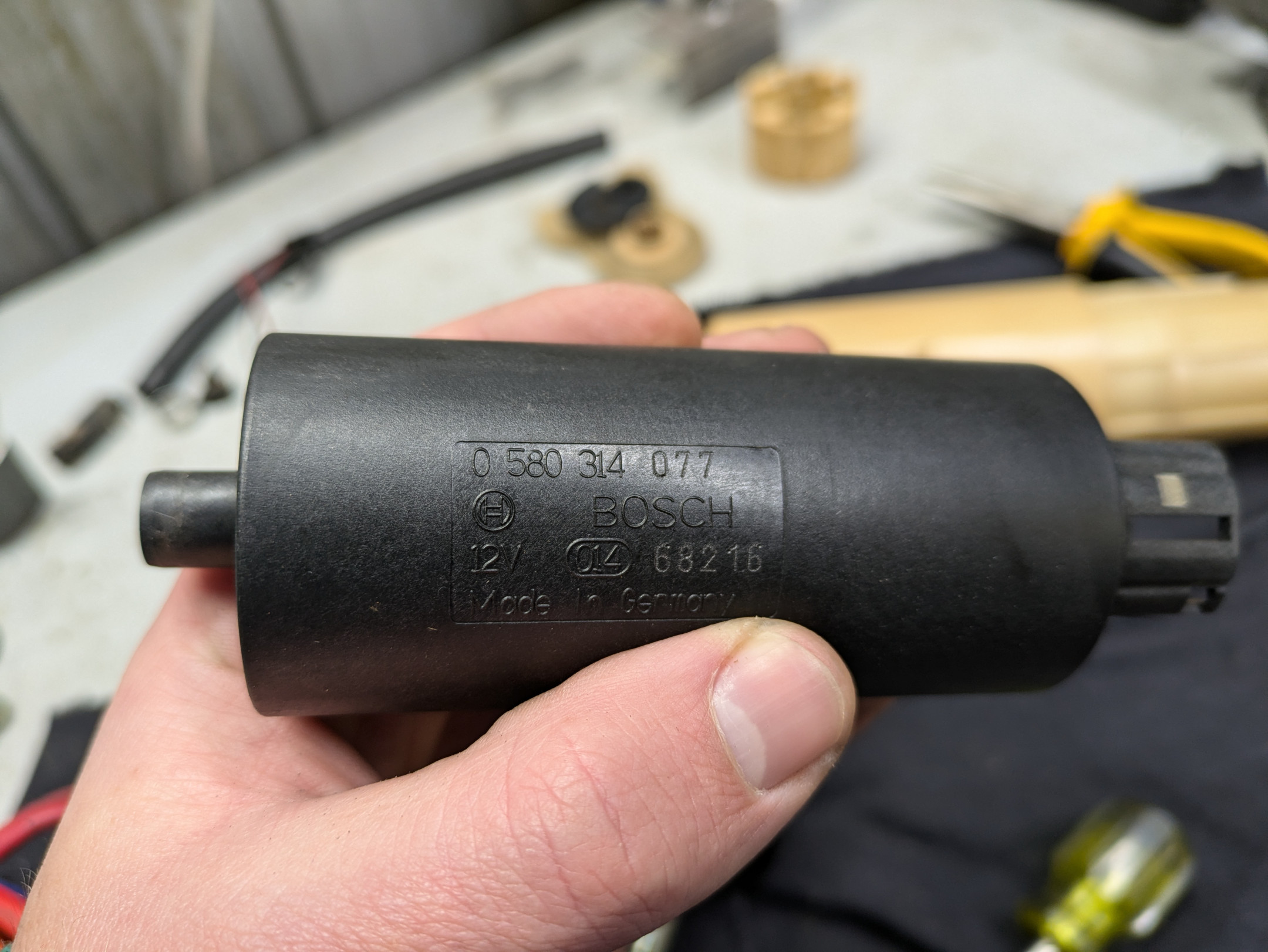
The in-tank fuel pump was replaced with a high-pressure unit at some point, likely when the previous owner turbo’d the car on the old engine before that was ripped out and the shell was sold to me. I was under the impression it was stock, and I put a high-pressure unit under the car. Turns out that’s probably been unnecessary the whole time, but meh. In-tank fuel hose was marked as 1995.
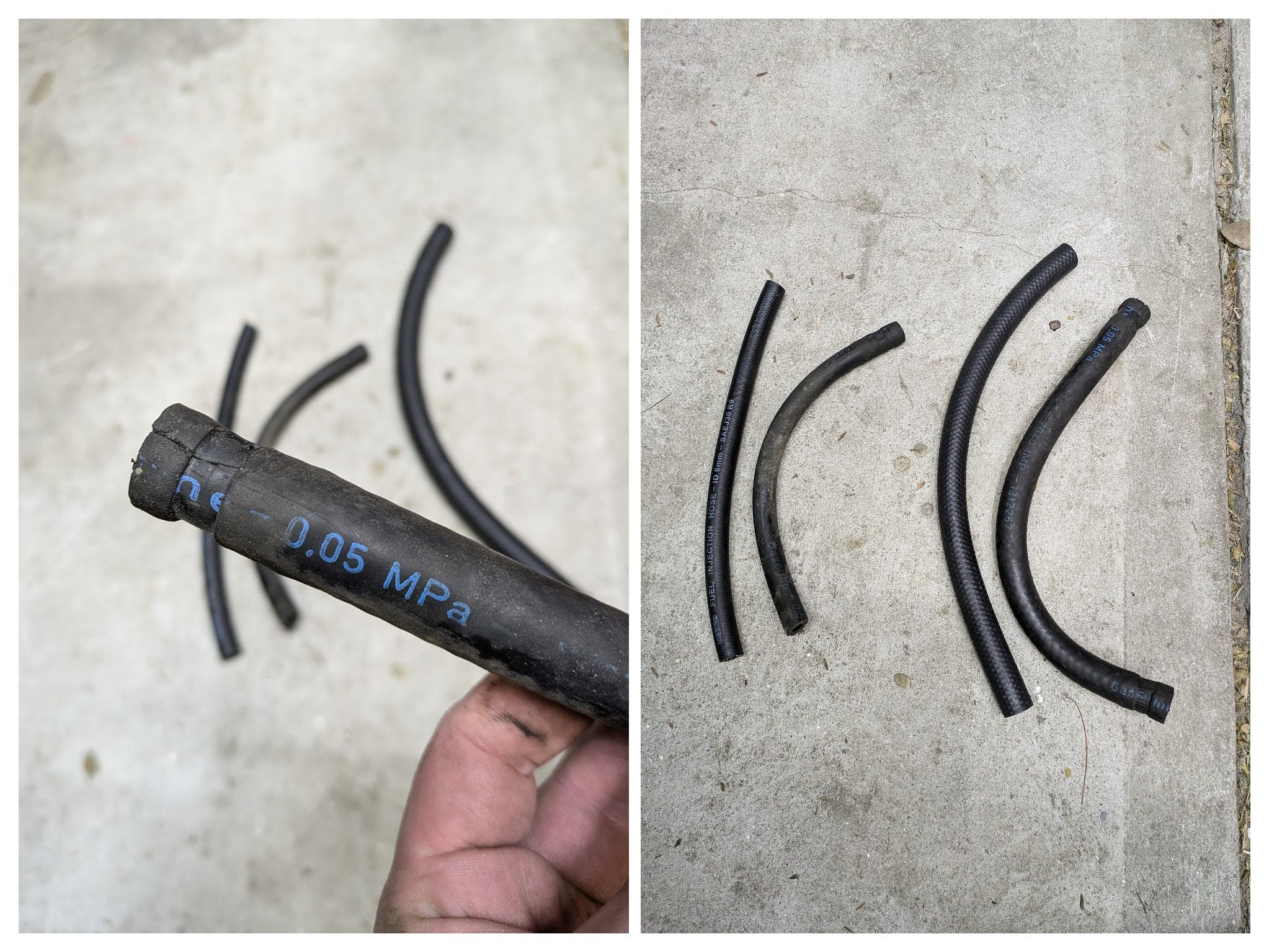
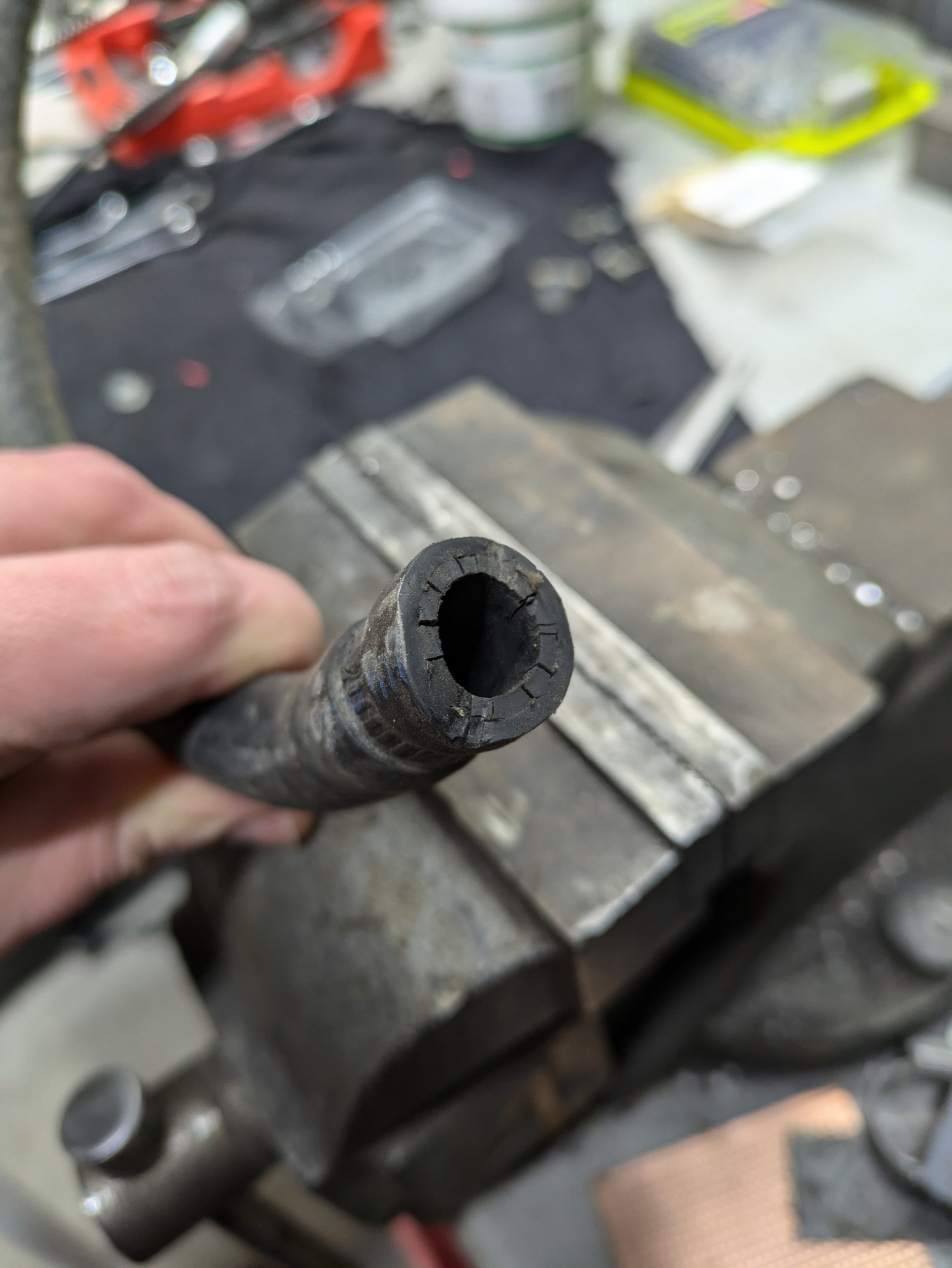
Though the pump was upgraded to a high pressure unit, the 11mm fuel hose coming out of the tank was not rated for high-pressure, but was the original 0.05mpa (i.e. ~7psi) hose originally on the car. It was marked as 1993, so original, and was cracked at the ends. I’m pretty glad it didn’t burst and set things on fire.
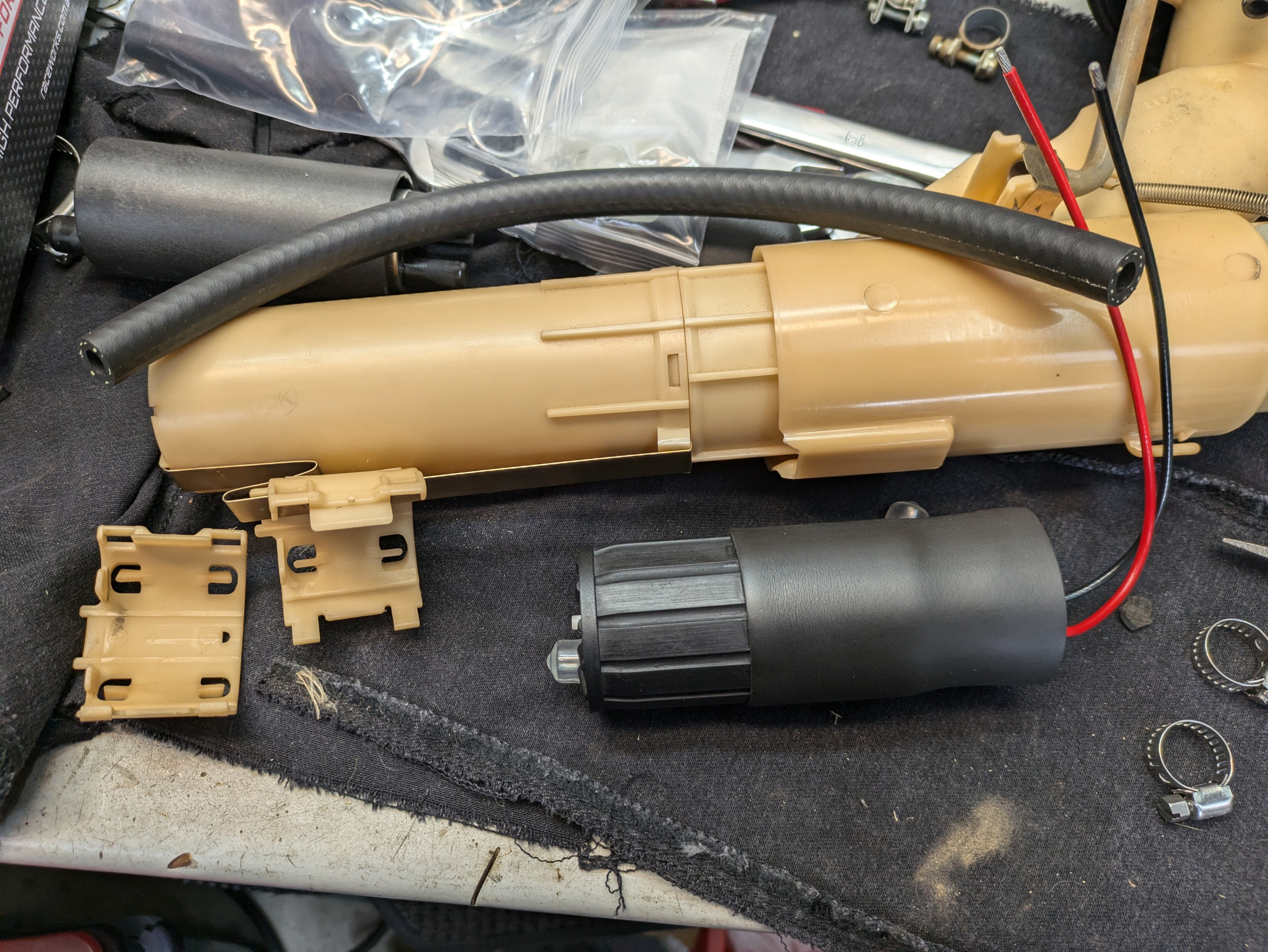
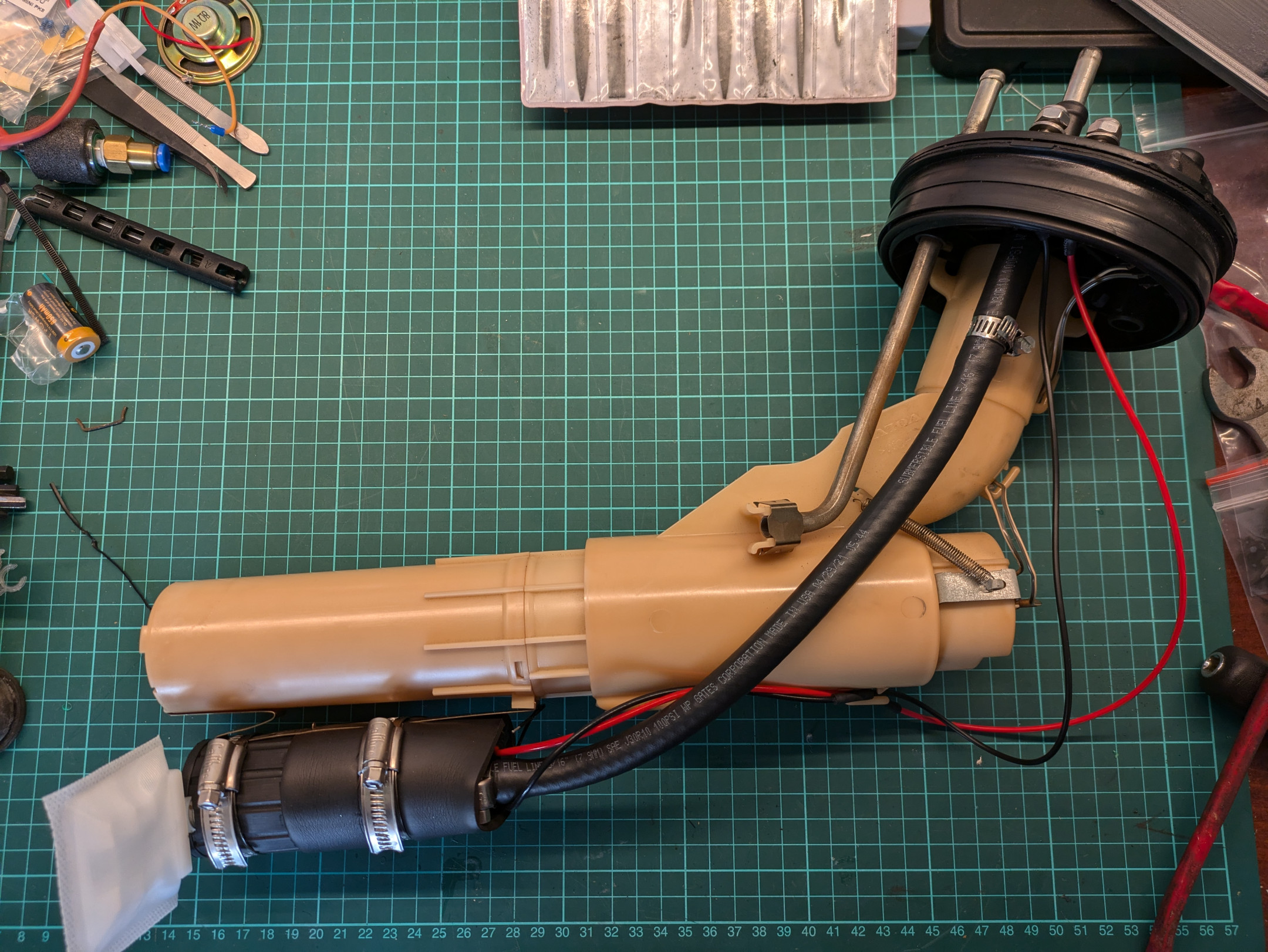
The old pump was removed from the hanger, and the Raceworks pump was installed, securing it with hose clamps in the original position. I tried using the plastic cage used on the bosch pump but I wasn’t happy with how it fitted. With the sock fitted, it was time to splice the wires to extend them to the bulkhead and plumb it all up before putting it in the tank.
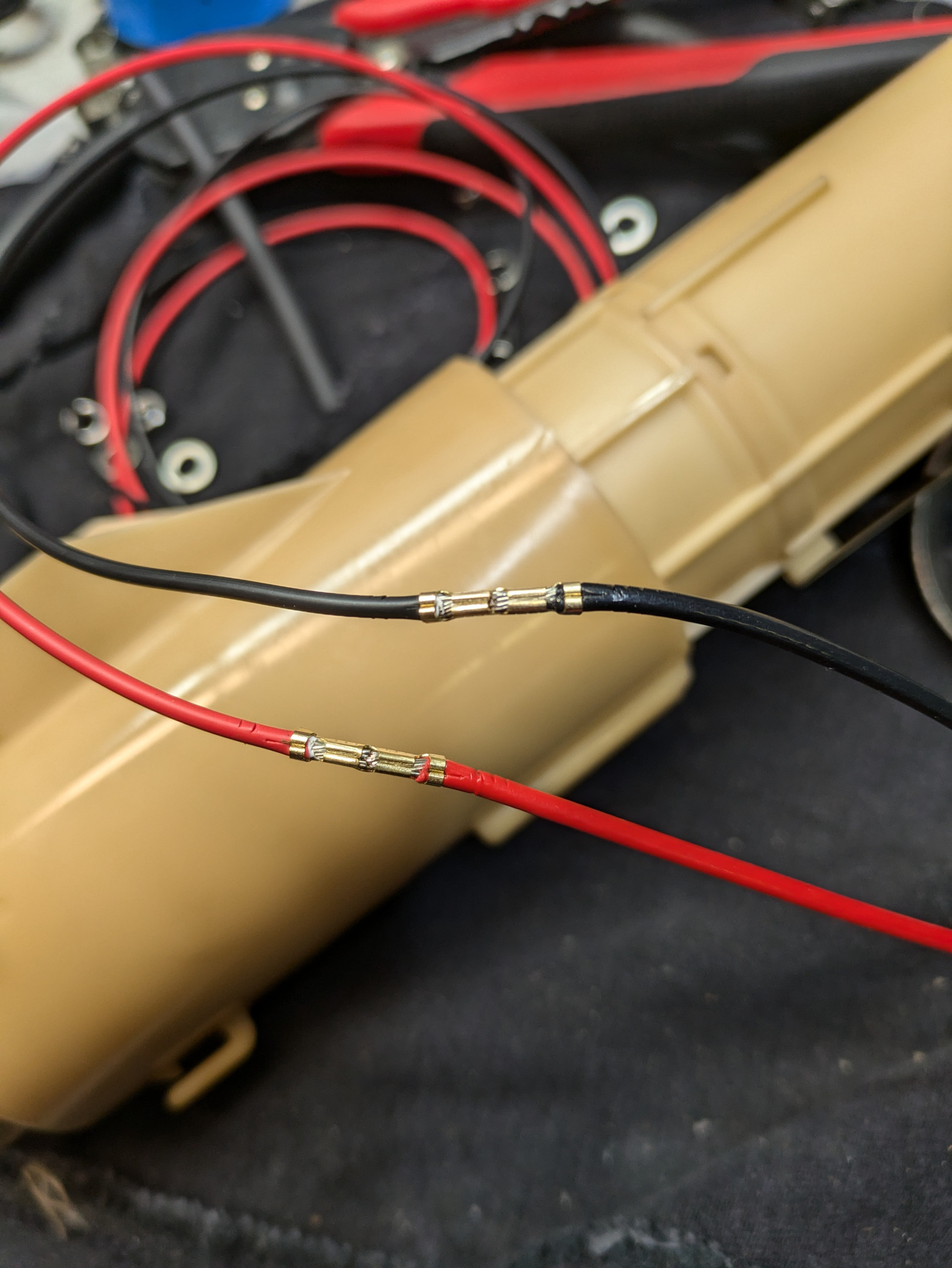
It was then covered with fuel-safe raychem heatshrink.
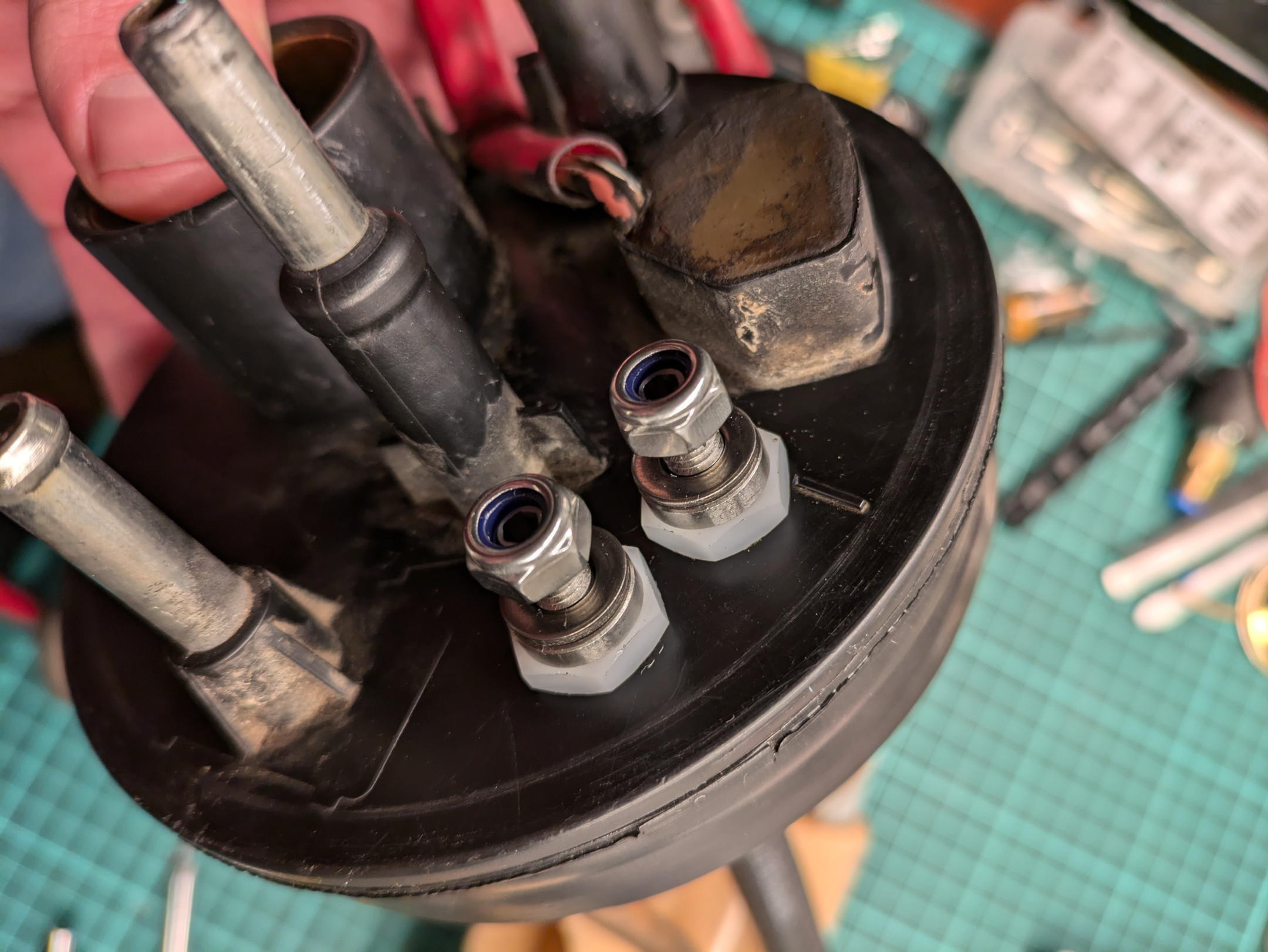
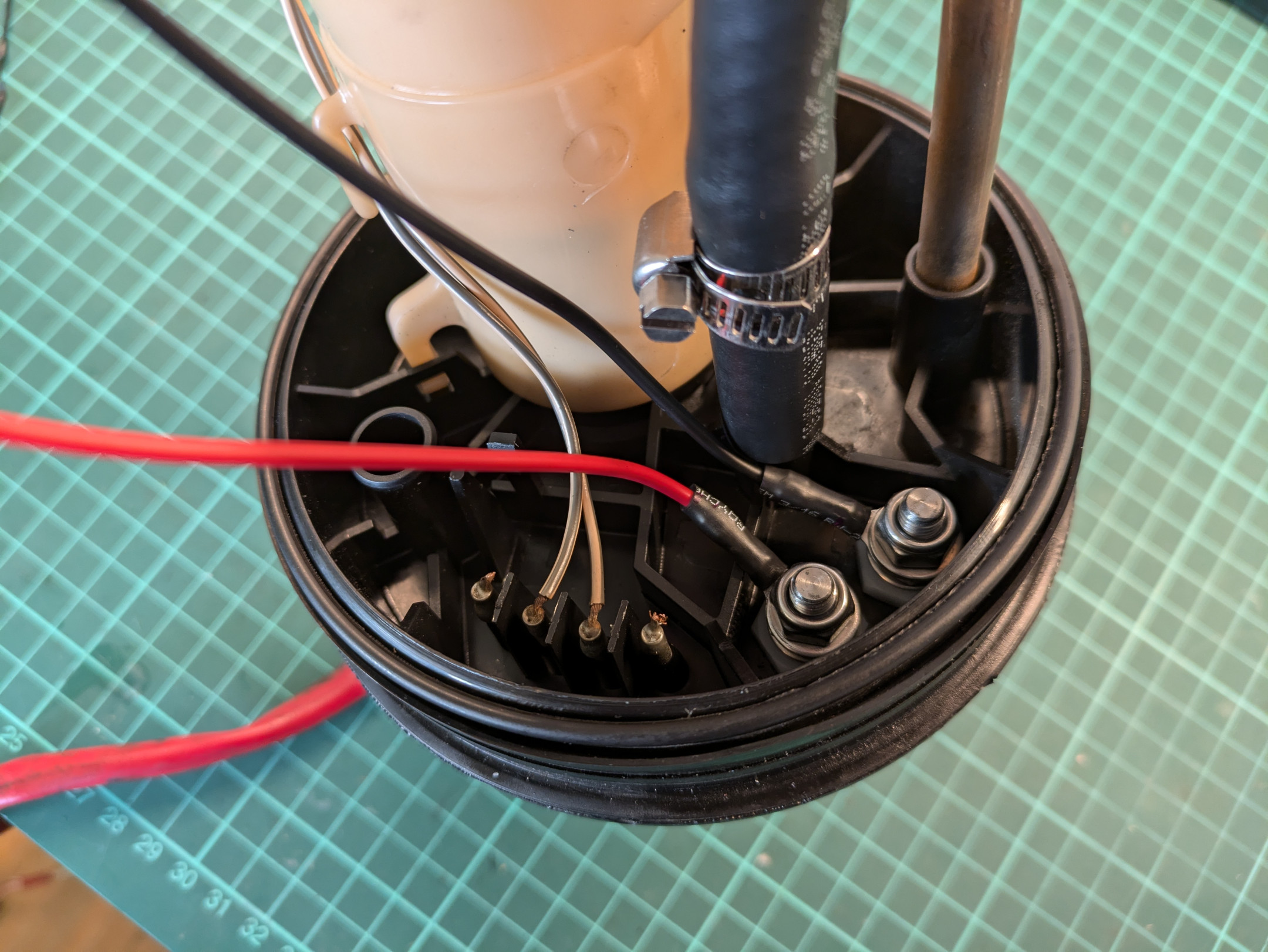
The raceworks high-current bulkhead connectors were installed after drilling two holes in the lid, and then it was all secured, ready for install.
The old under-car fuel pump and filter were removed, and a new (stock spec) filter with the right AN fittings were installed in the original location.
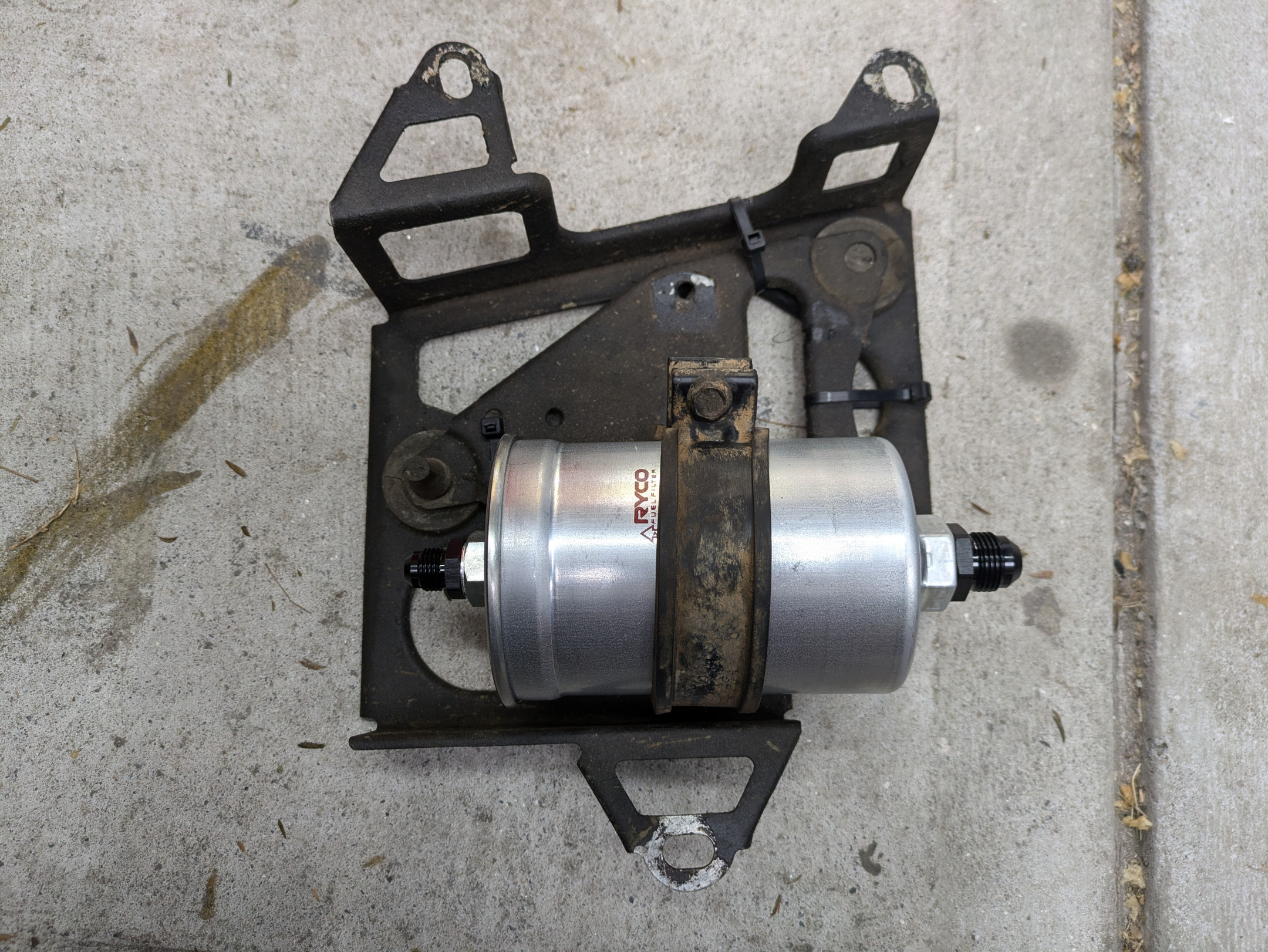
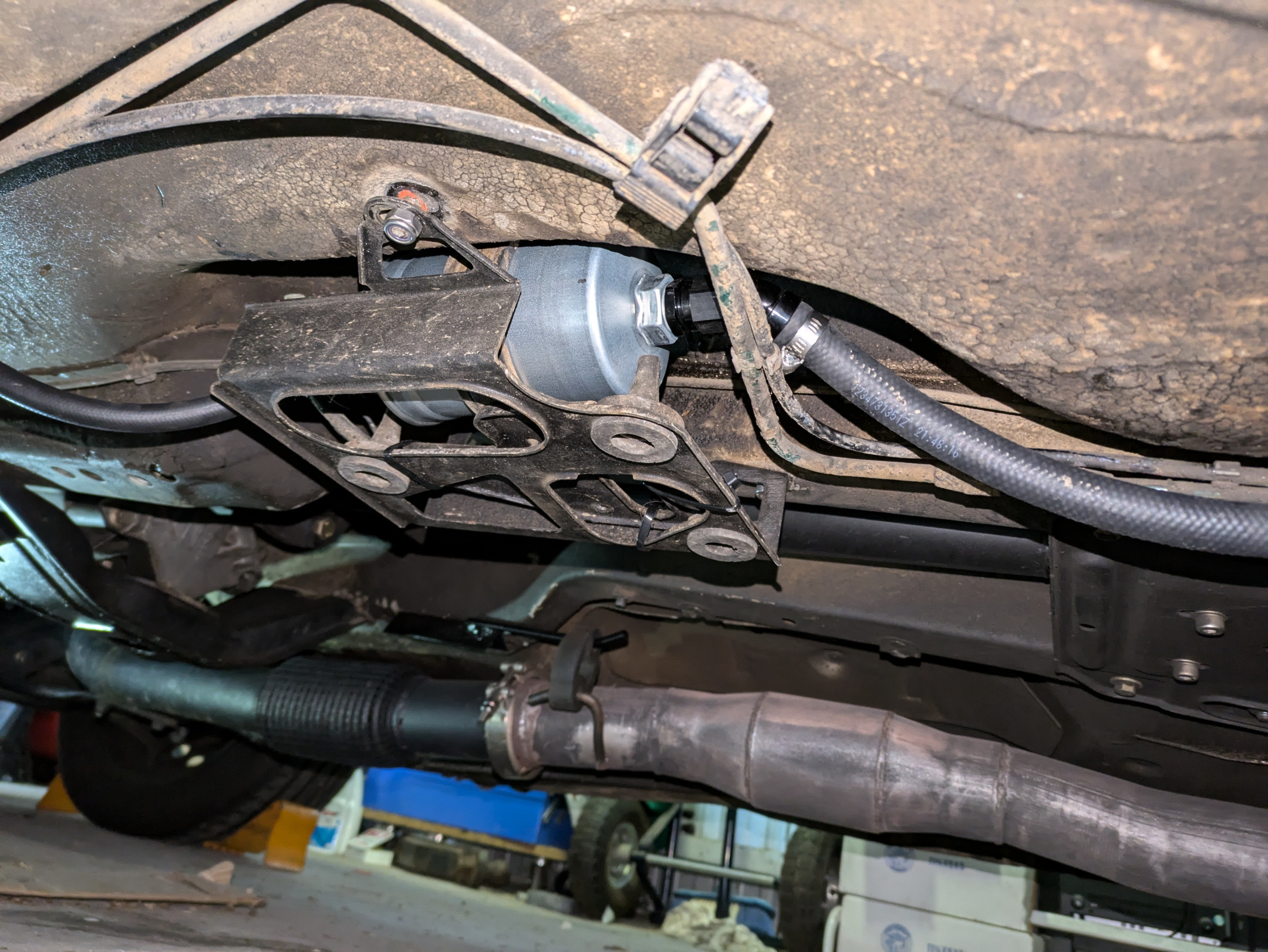
The new 5/16" (8mm) hose was then run up to the rail, and the return hose was replaced too. Everything except the hose connecting the rail to the reg is new, and I'll do that last piece shortly.
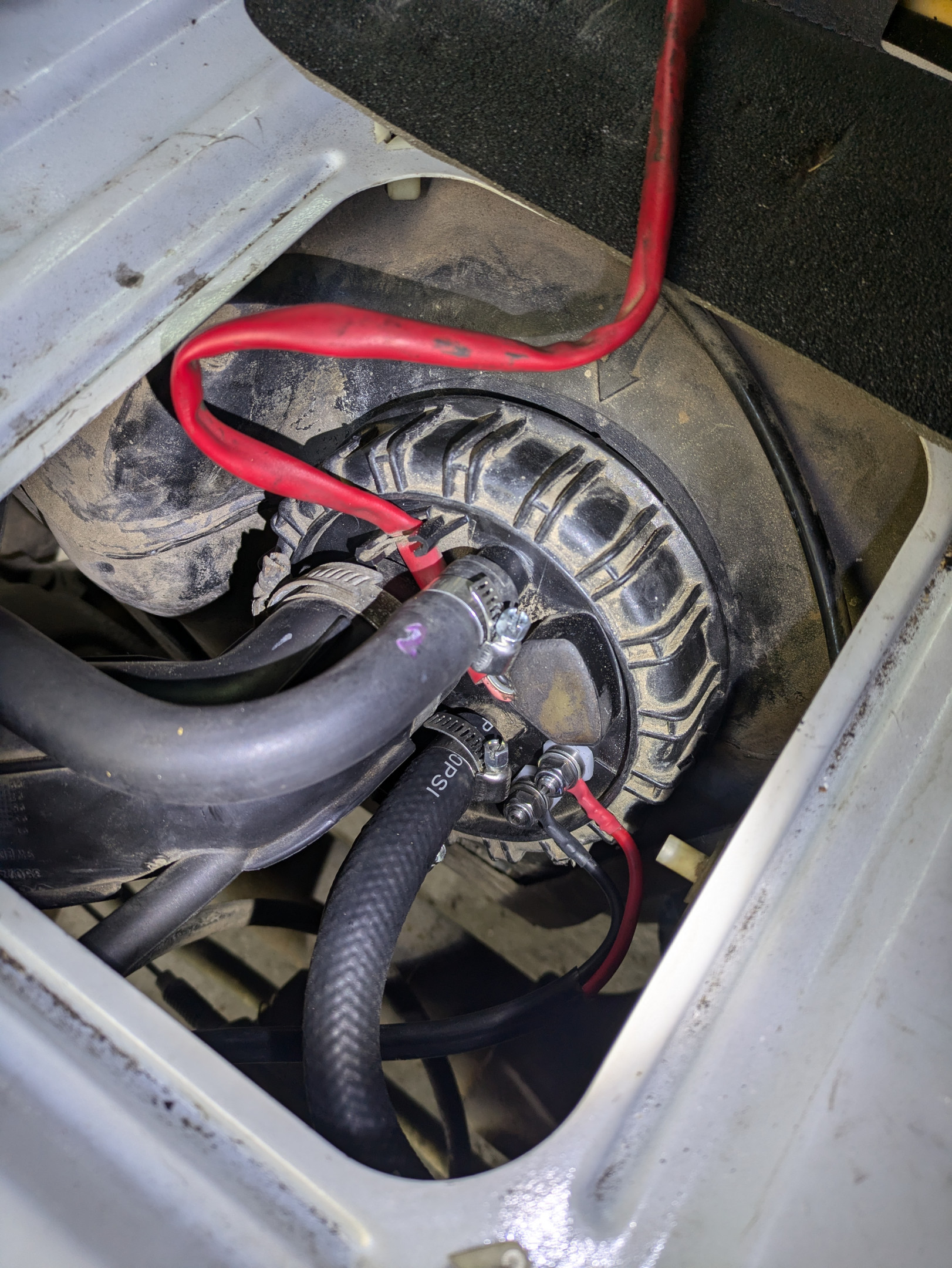
After some swearing, the carrier was installed back in the tank, new hoses were connected and the filter, and new feed/return lines were installed. It's a bit of a pain to run the new hoses to the hard lines near the tank, but I'm glad I did given the condition of the old main feed hose. Tank vent hose looked in fine condition so didn't replace it.
I ran new 12AWG wire from the tank bulkhead connector all the way (~6 meters?) to the connector that originally powered the under-car pump.
I put some new fuel in and it started up first crank, and no longer dies after moving around like it did. So far so good. Noticed there’s less power draw on the electrical system too with the voltage it sits at idling now. Clearly having two high-pressure pumps was putting a bit more load on it, and a single pump removes a point of failure so that’s nice.
The best part? After some laps of the block, I realised the stumble I had coming onto boost is completely gone now, and it just freight trains. It’s completely different now I wonder how long it’s been on its last legs for. Very occasionally if I drop a gear and give it a boot my UTCOMP gauge would beep at me warning me of a lean condition (monitoring AFRs while in positive boost), at which point I immediately back off, but I thought it was possibly a lag between sensors. Fingers crossed that issue is solved too and that no damage was done to the engine because of that.
After it was all buttoned up, I had an issue where the fuel level was stuck at the previous position, and immediately I thought it might be an issue with the float inside the housing that got stuck. I decided to brim the tank, go for a long drive in it and by the halfway point about 100km in, it had sorted itself out and reads properly again! Feels good.
Edit: OH and there's even LESS cabin noise now, since that noisy-as-hell under-car pump isn't there anymore. I can't believe how much of a difference that alone made.