I got a little further today.

I dug out the engine stand.
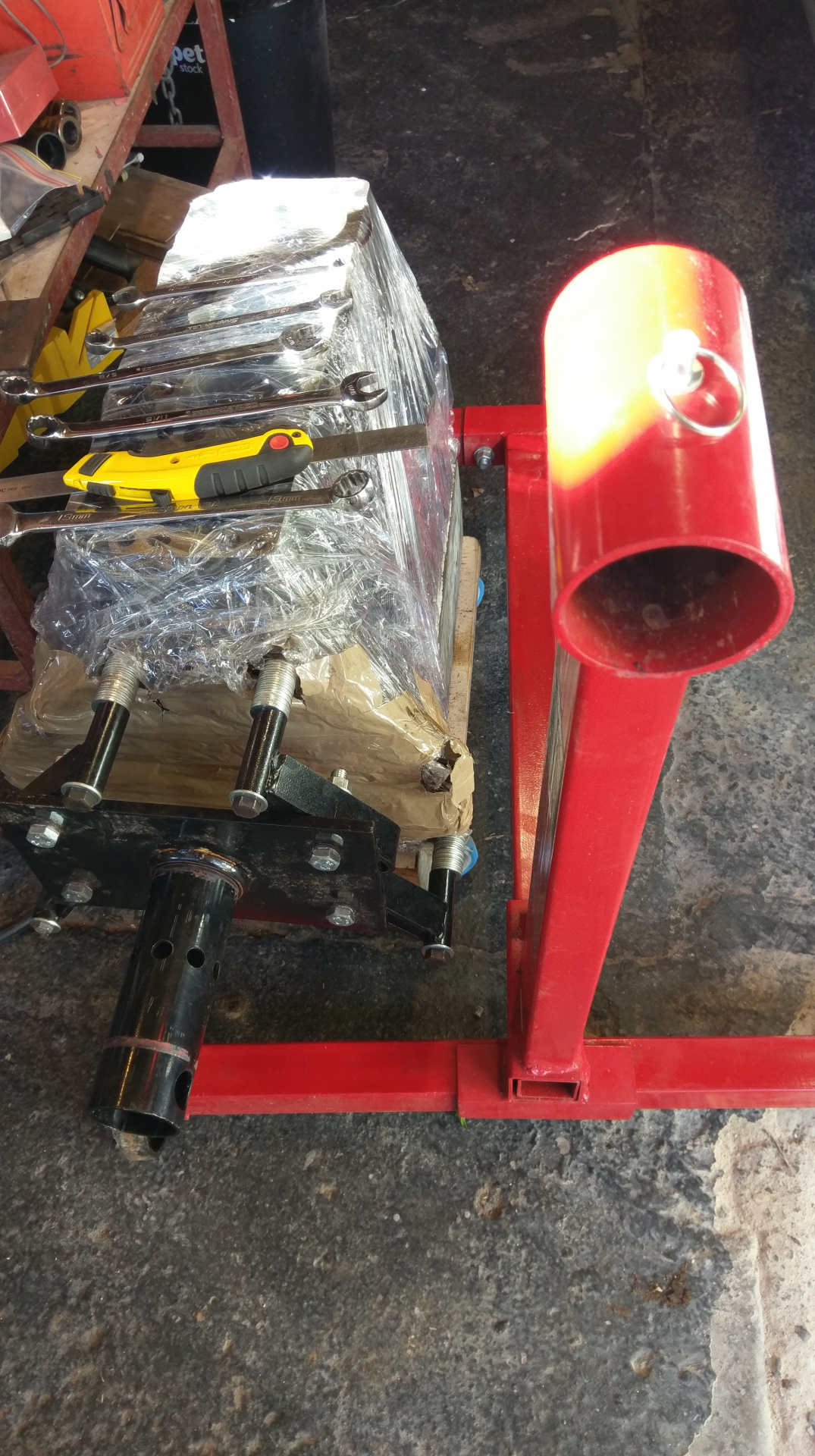
Got it mounted to the block.

With some help from my better half to lift the assembly in place.

I wiped down the main journals with acetone and blew with compressed air. The block is pretty clean as I got the machine shop to clean and wrap. Worth the sixty bucks.

Main shells in the block.

It came cleaned but oiled. Wiping down with a soft clean rang and acetone and blowing clean including the oil ways. the edges of the oil ways have been nicely deburred. The efforts of balancing can be seen with the linishing marks on the first counter weight and near no.4 big end journal.

the main seal surface doesn't look great. I hit it with some 1200 wet and dry and metho.

That's a bit better. I will have to remember to leave the main seal proud so the seal runs in the best area.

It can be seen in the last two pics that the thrust surfaces only just cleaned up.

On the uncleaned rear main housing where the seal last sat. It should be ok to leave it proud by a mm or two.

Extracting the spigot bearing without a puller. Grease (or bread if the grease gets though the sheilds) and a punch works fine too.

Giving the flywheel mounting surface a light stoning to ensure there are no raised burrs or dings.

Giving all of the journals another clean with acetone and a soft cloth.

Adding some assembly lube and oil to the main shells in the block.

Gently placing the crank where it is supposed to be.

Adding some assembly lube and oil which I mix into a slippery goop with my finger.

All the main caps on and just nipped up. I turns by hand, which I guess is a good sign. I discussed with the machine shop if I should plastigauge it or not. The response was, if the were gong to assemble it for me the consider it fully measured and wouldn't themselves. They did assemble, torque and measure the bearings and grind to suite.
That's it for today, back inside to find the torque settings.

Hopefully tomorrow I will have time to get stuck into putting the rods/pistons in.
Thanks,
-Todd