I bought a 1966 light green 2 door 122S about 14 years ago (to go with the other three 120's that I had.....
I started this project around 10 years ago, having been inspired to build it as a 'race car' after seeing Andrew Whites 122 at Targa Tasmania (on display with all the other entrants at Launceston's Silverdome).
Since all 18 month projects always seem to take at least a decade to get together, I am now at the stage of having something to show for my labours, though it is still not quite finished (but is at least starting to look like I am close(ish) to completion......
I started by stripping the car to a bare shell and setting it up on a homemade rotisserie.
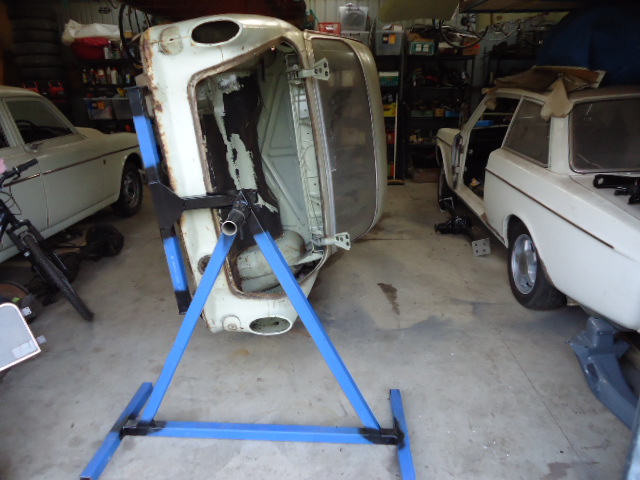
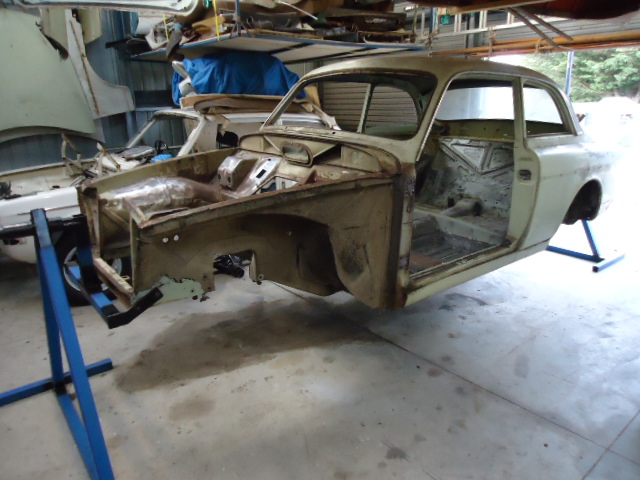
This was a far as I got for a few years, as I first finished off the 142 that you can see in the background, and also my 122S wagon. I also setup a 240 as a rally car that I competed in the Historic Rally Association standard car class with. Lots of fun, then covid came along. This finally got me back to the 122S rally project.. I upgraded the rear suspension pickup points to that of the 1968 onwards cars, the bits having come off an almost totally stuffed 1968 wreck that I acquired many years before.
I strengthened the chassis at the front and rear, and had Damon at Geelong Motorsports Fabrication install a 'national spec' roll cage into the car, i was very pleased with the result.
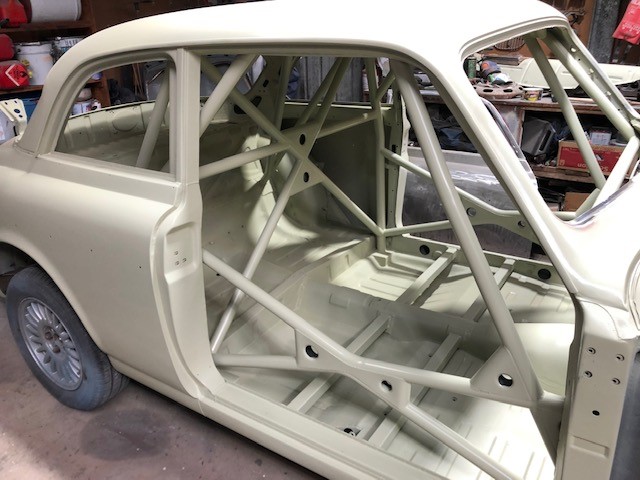
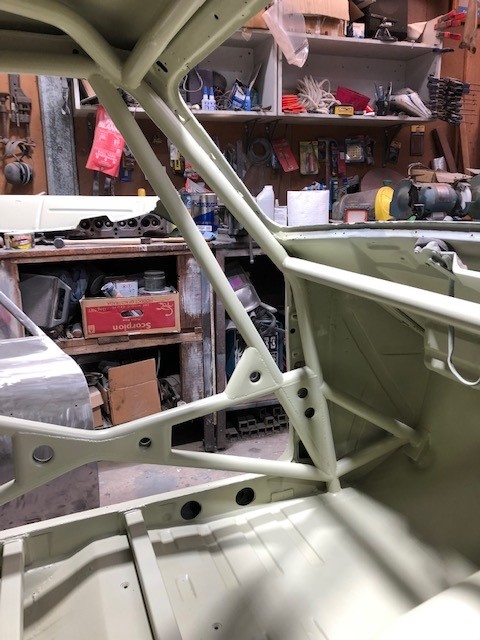
I managed to get a hold of an 1800ES rear end and associated front end bits, and they are now in the car, giving me four wheel disc brakes.
Progress on the car has now advanced to the following:
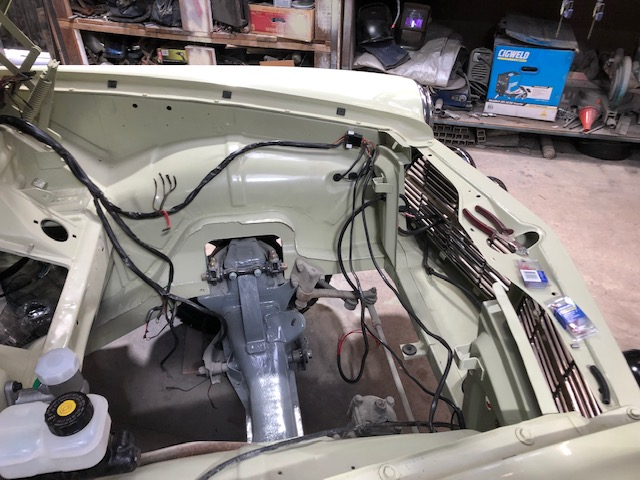
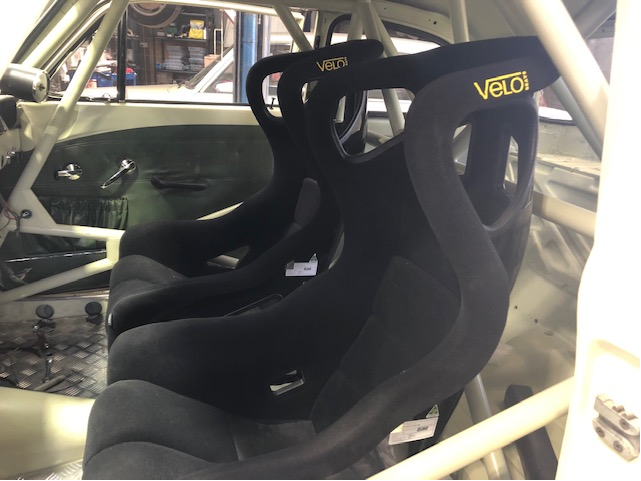
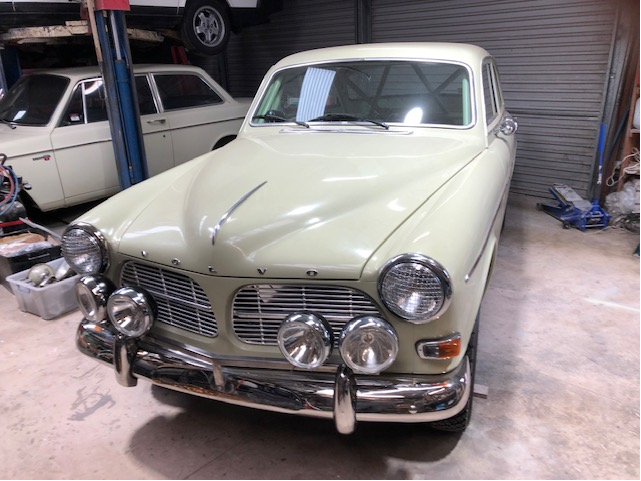
I got the engine block, crankshaft and flywheel back from North Geelong Engines last week, and have been putting the engine together. I have used forged pistons, Tinus tuning connecting rods and their rally cam, steel timing gears etc. Head has been ported (by me ?) and using 46 mm inlets and 38 mm exhausts.
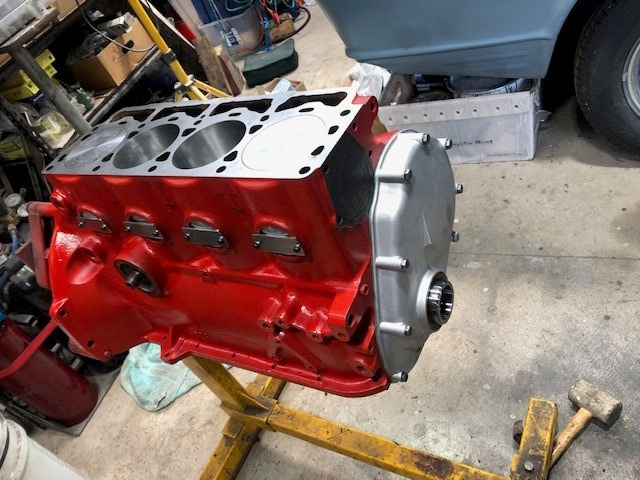
Hopefully the next few days will see it installed in the car.