Wow over a year ago I started this thread ? Been busy with life & things, and the car... Well I've been working on slowly but the bastard - something goes wrong every time.
Anyway I had been practising welding and fab for a while and as I was getting more confident, the list of things I wanted to make grew. I thought hey I want to give making a turbo manifold a crack. At which point I also decided I wanted to put the motor back in the slant position. I'll get back to the turbo manifold.
Last time I left off on making the intake and wiring... Wiring I've completed inside the cabin. Just need to do engine bay.
For the intake I ended up drawing a CNC flange in CAD and sent the file to china to be machined.
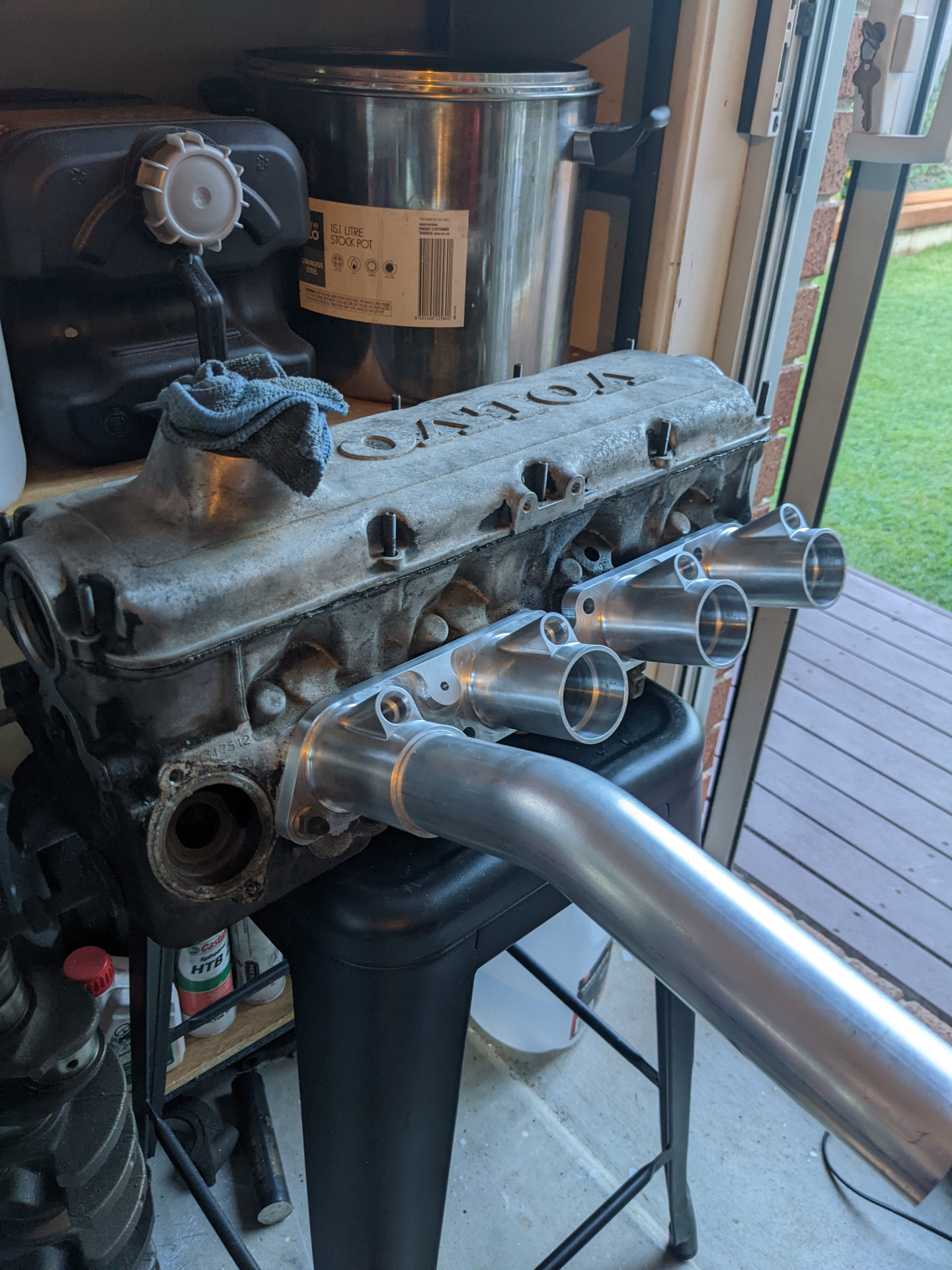
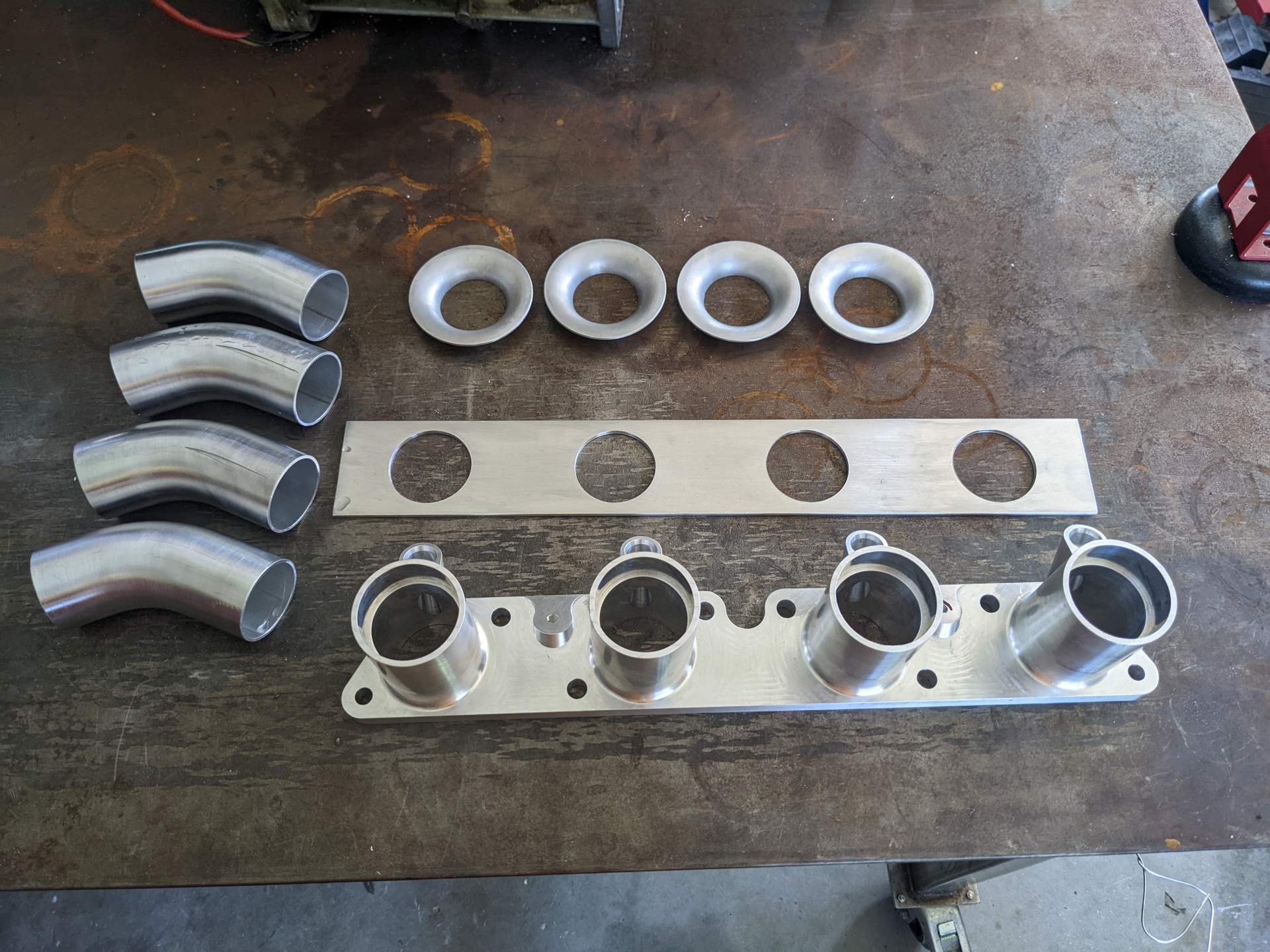
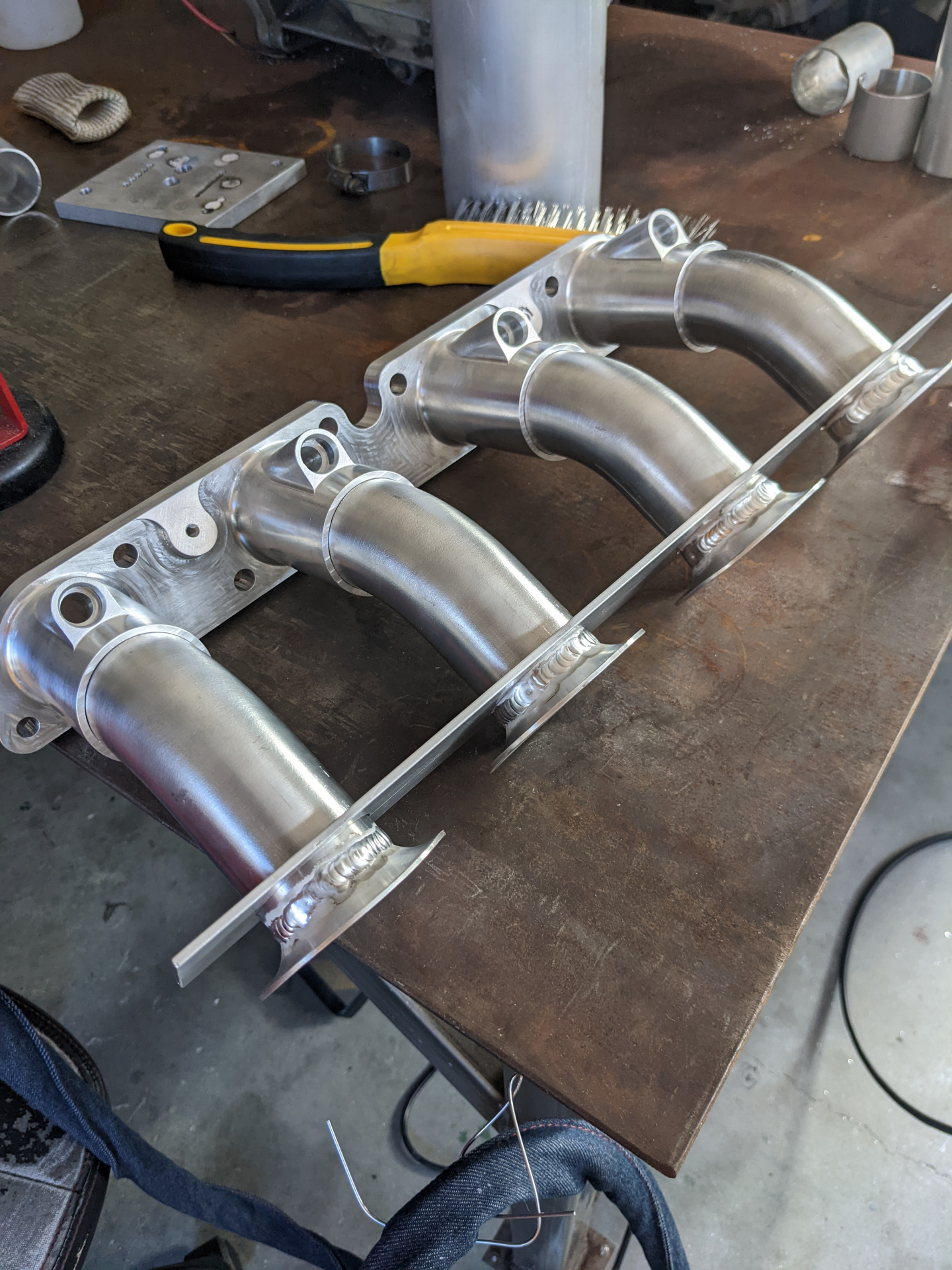
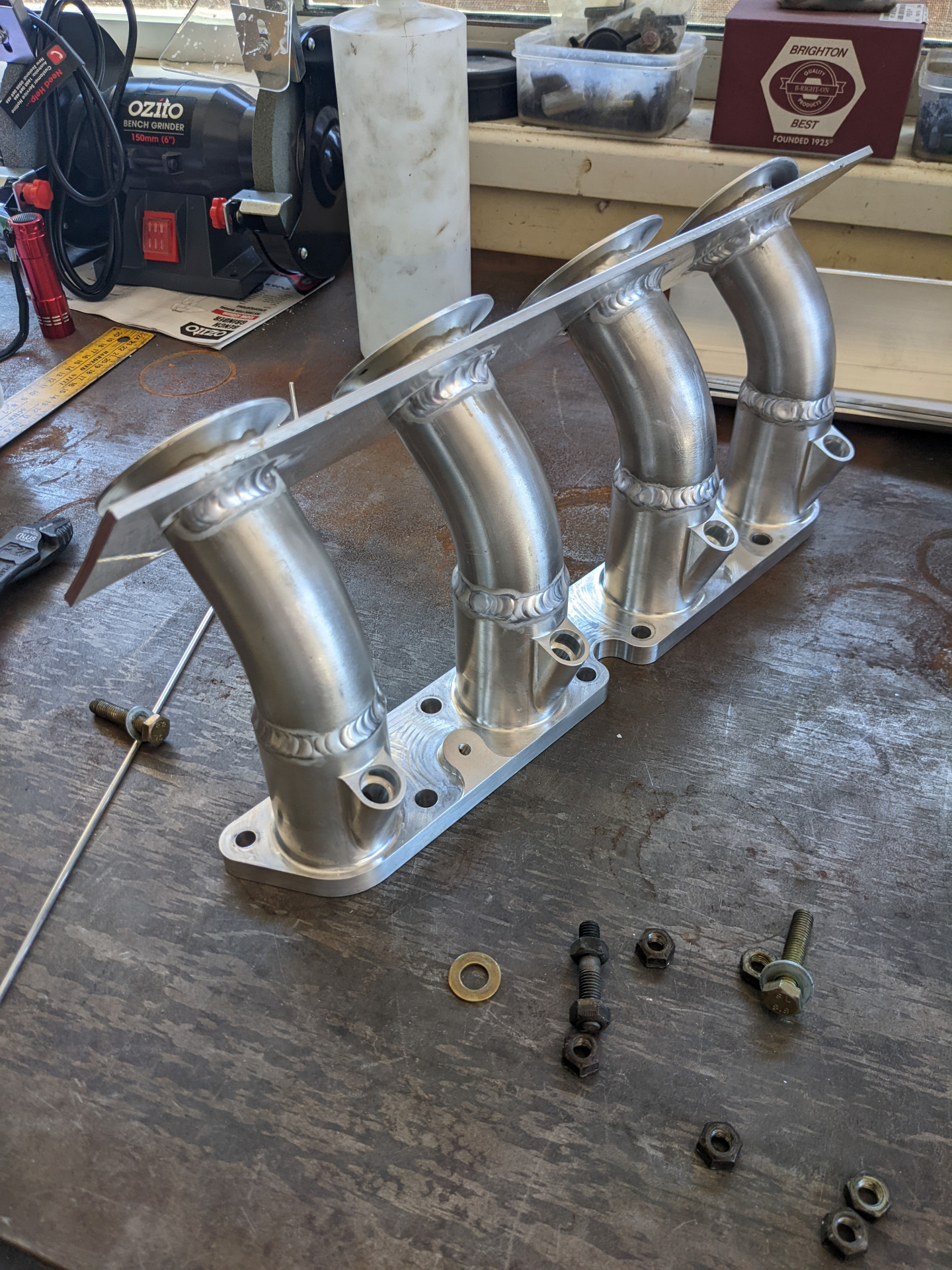
Long story short, while I was welding it up I got distracted and when I came back I wasn't watching myself and knocked it of the table doing this.
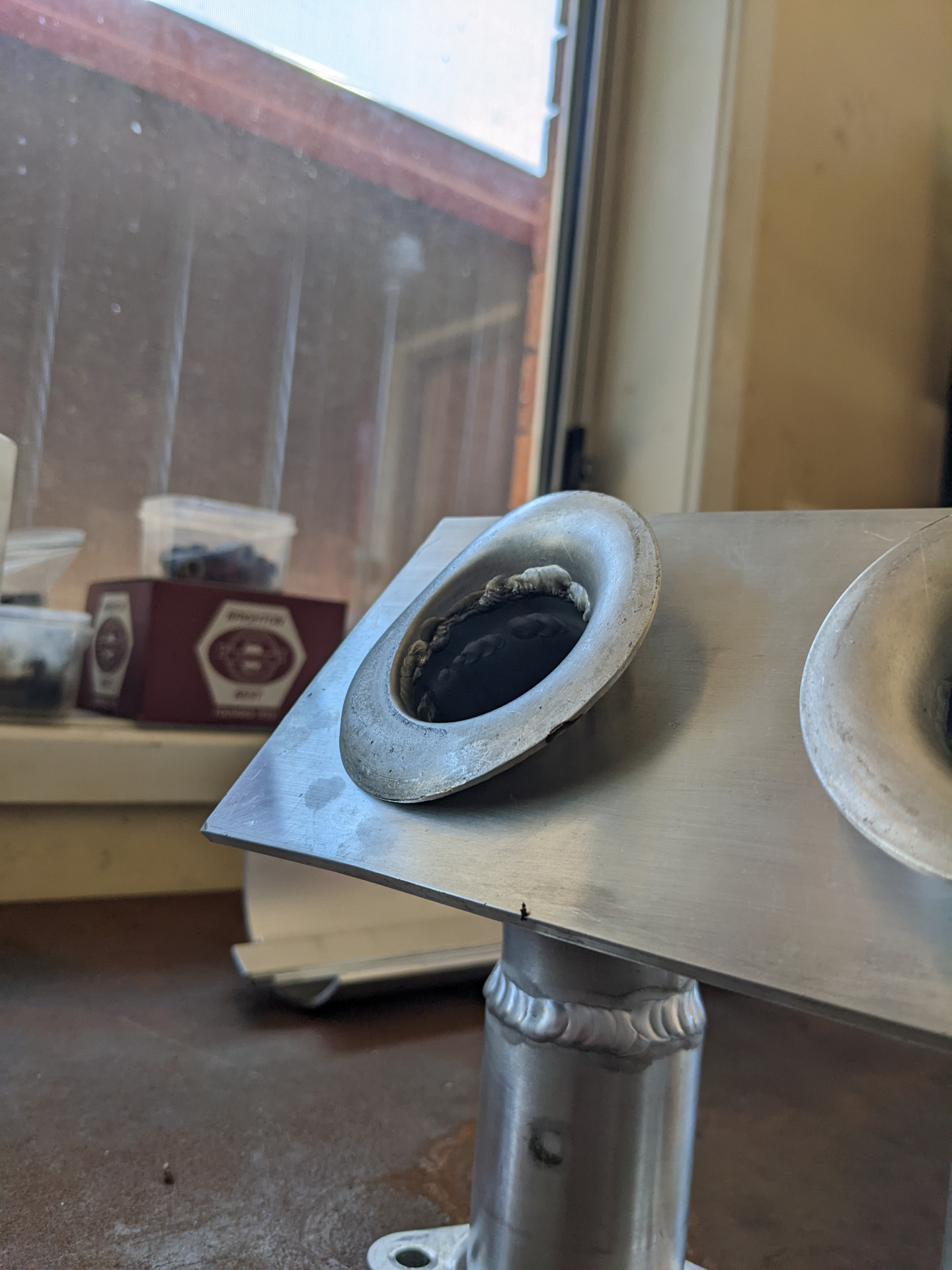
As of yet I haven't gone back to the intake, this was back in March this year. I will once I order some new material. I was frustrated to say the least.
In the mean time I've tackled the turbo manifold. I thought having a bottom mount setup would be pretty dope and allow for more room from the master cylinder & steering column but as you'll see I made things much worse and created more issues too lol. In the photos you'll see I started with one design then changed it to what it is now.
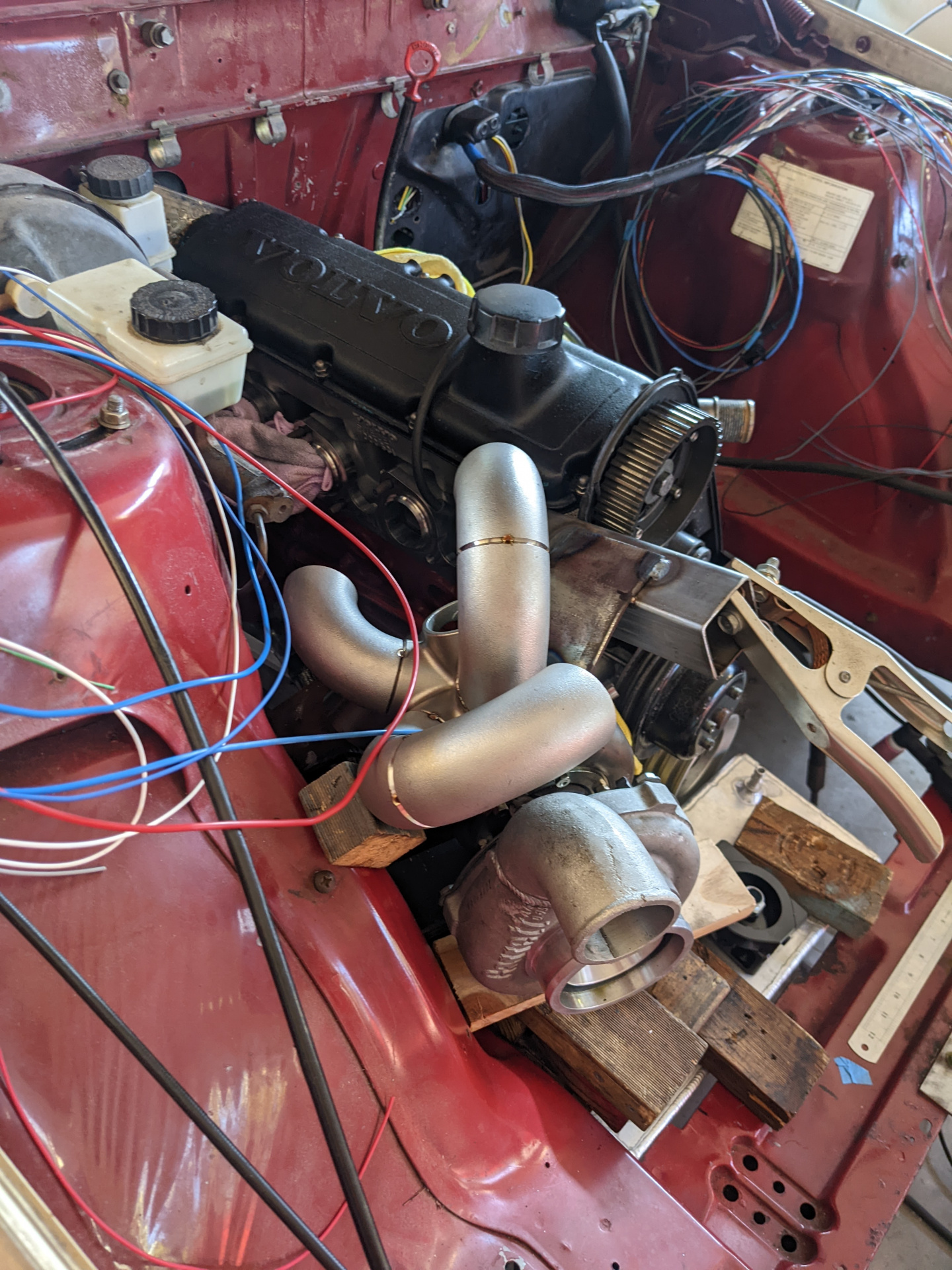
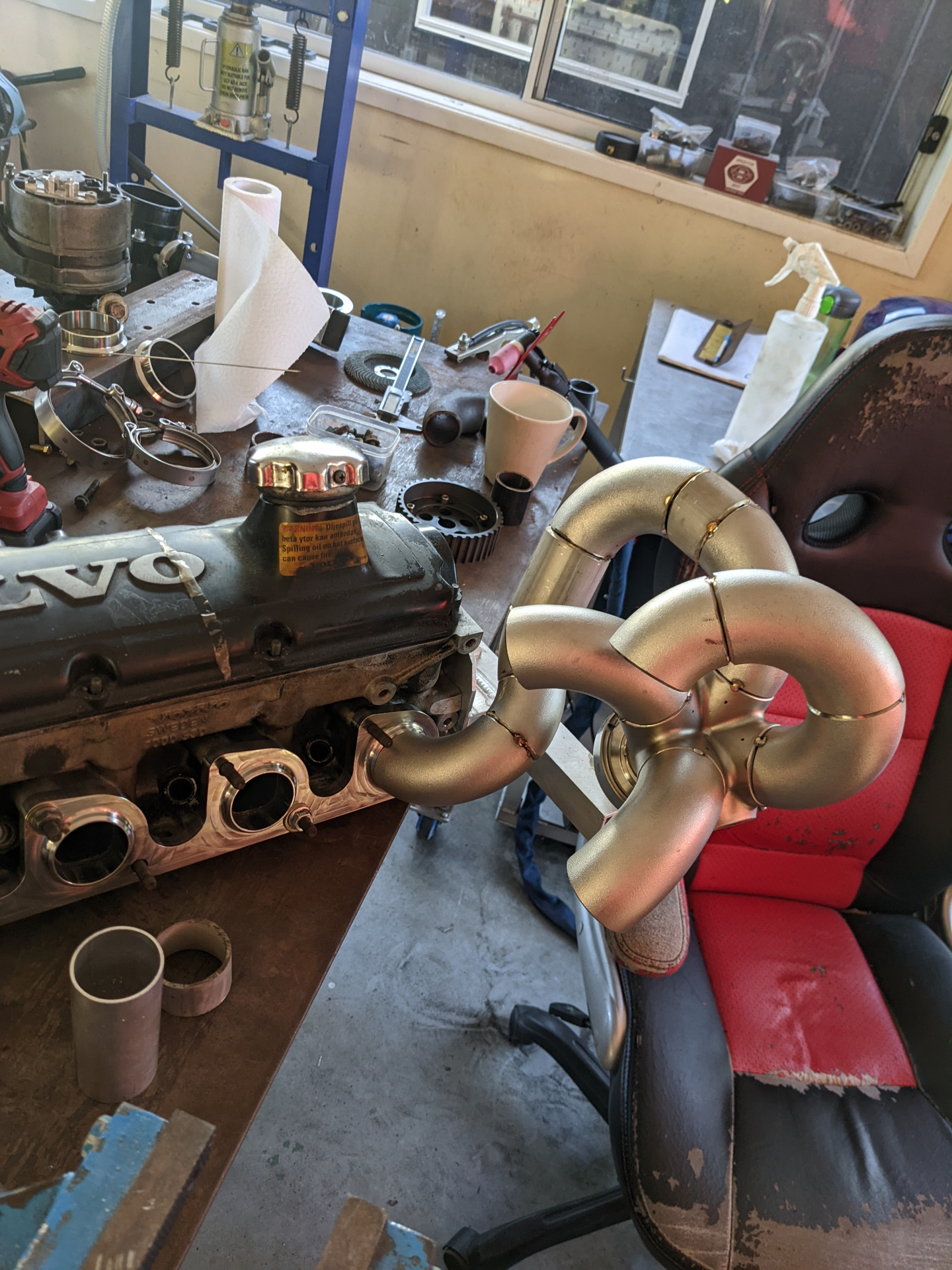
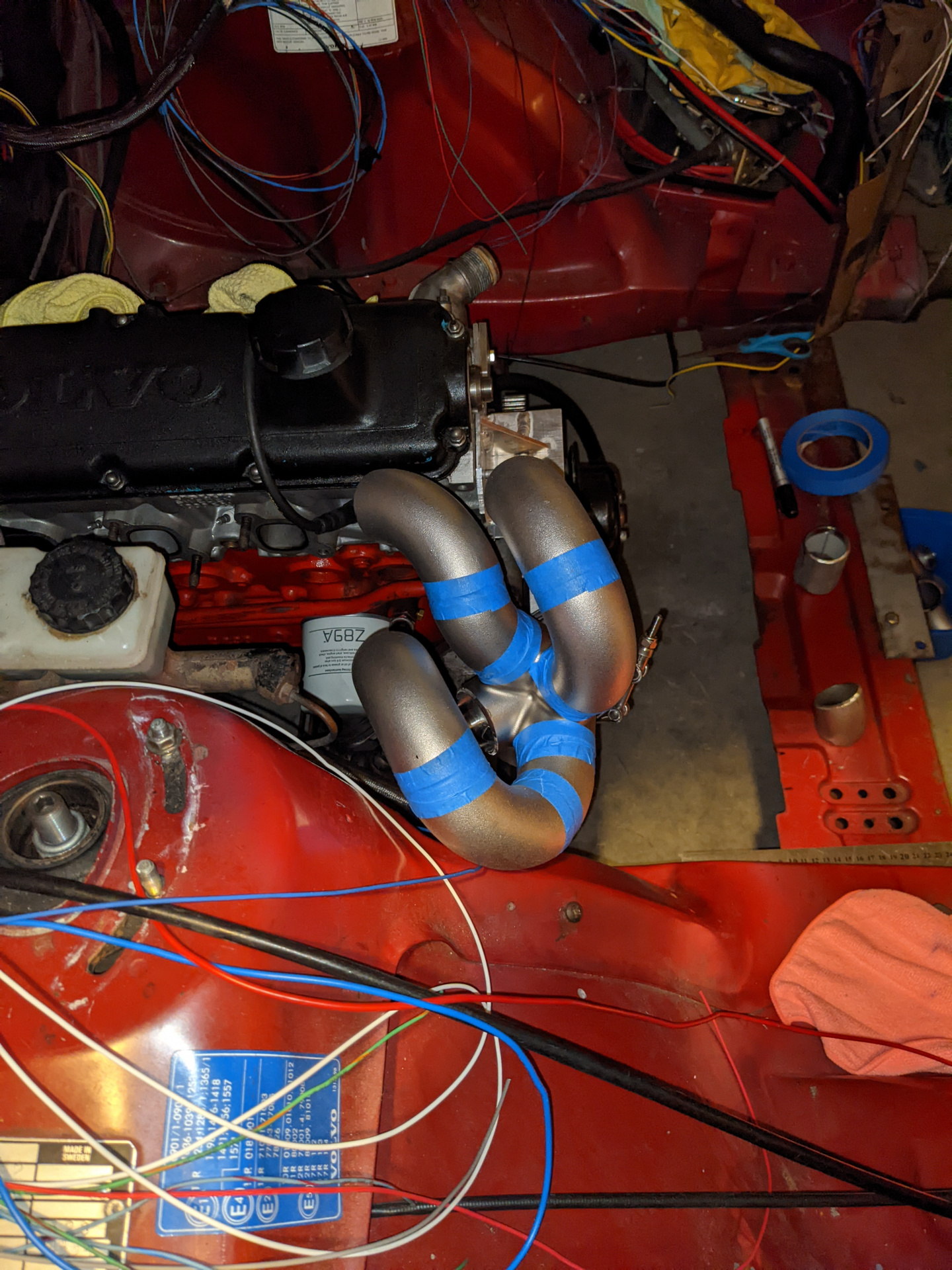
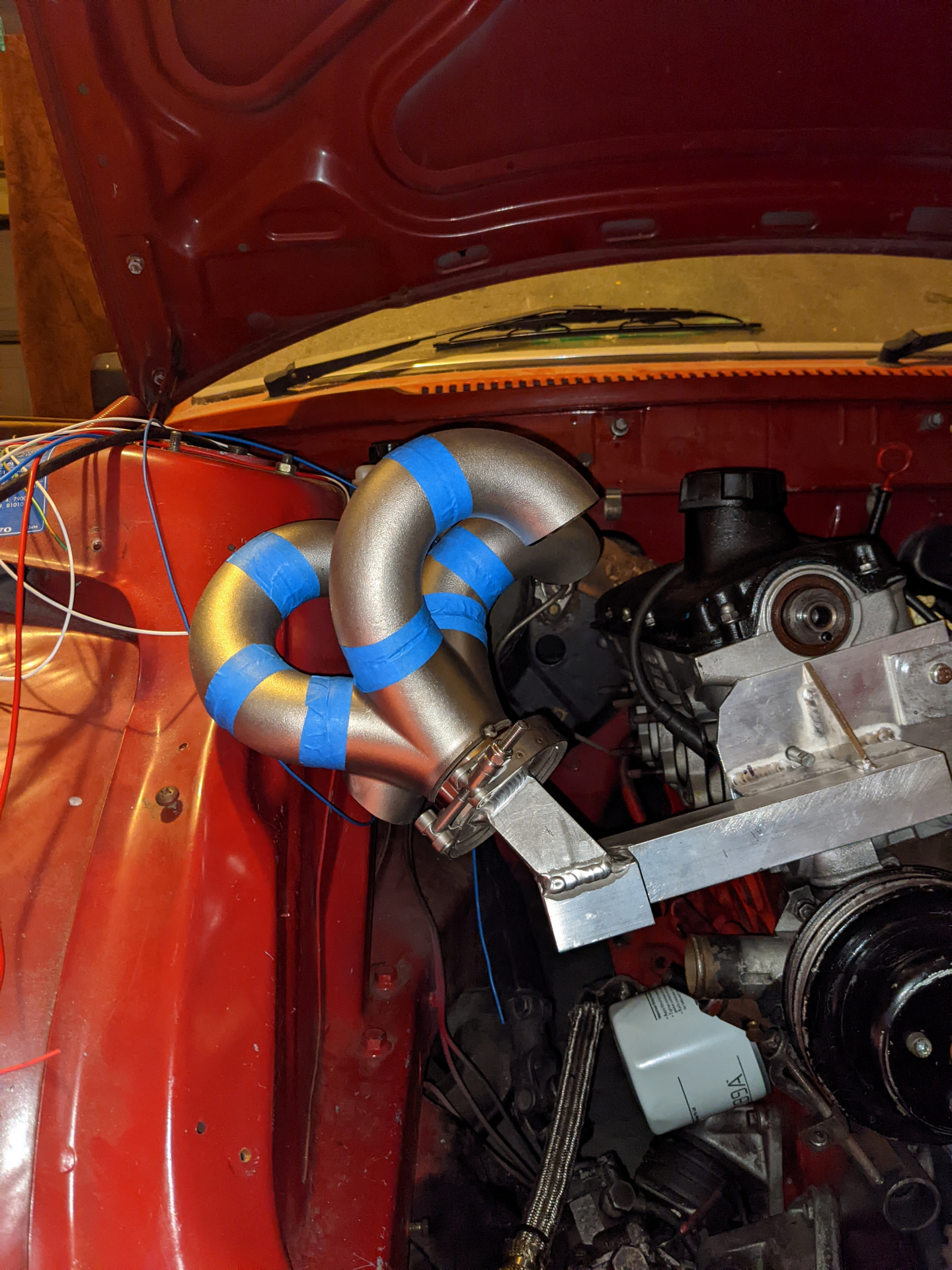
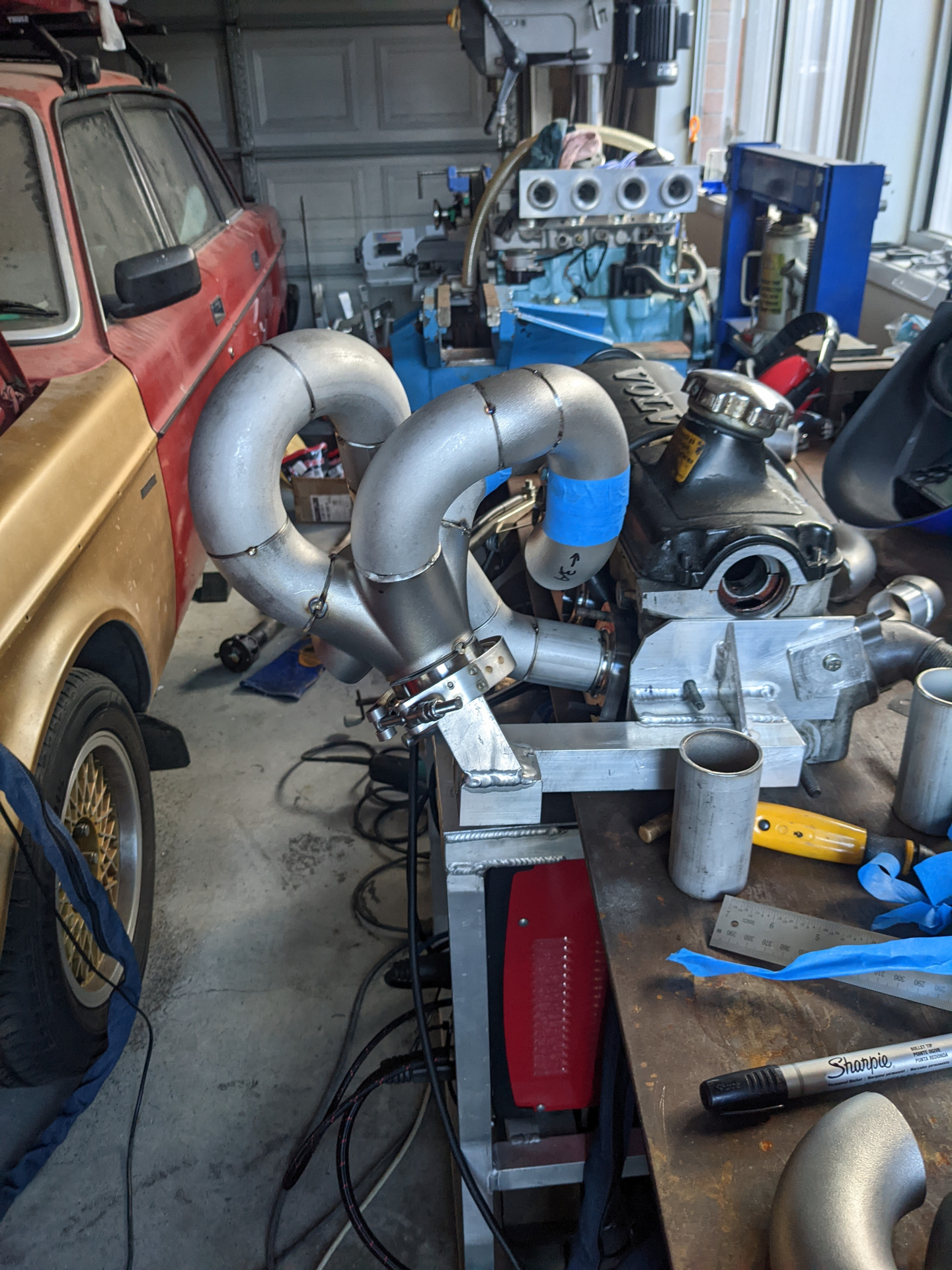
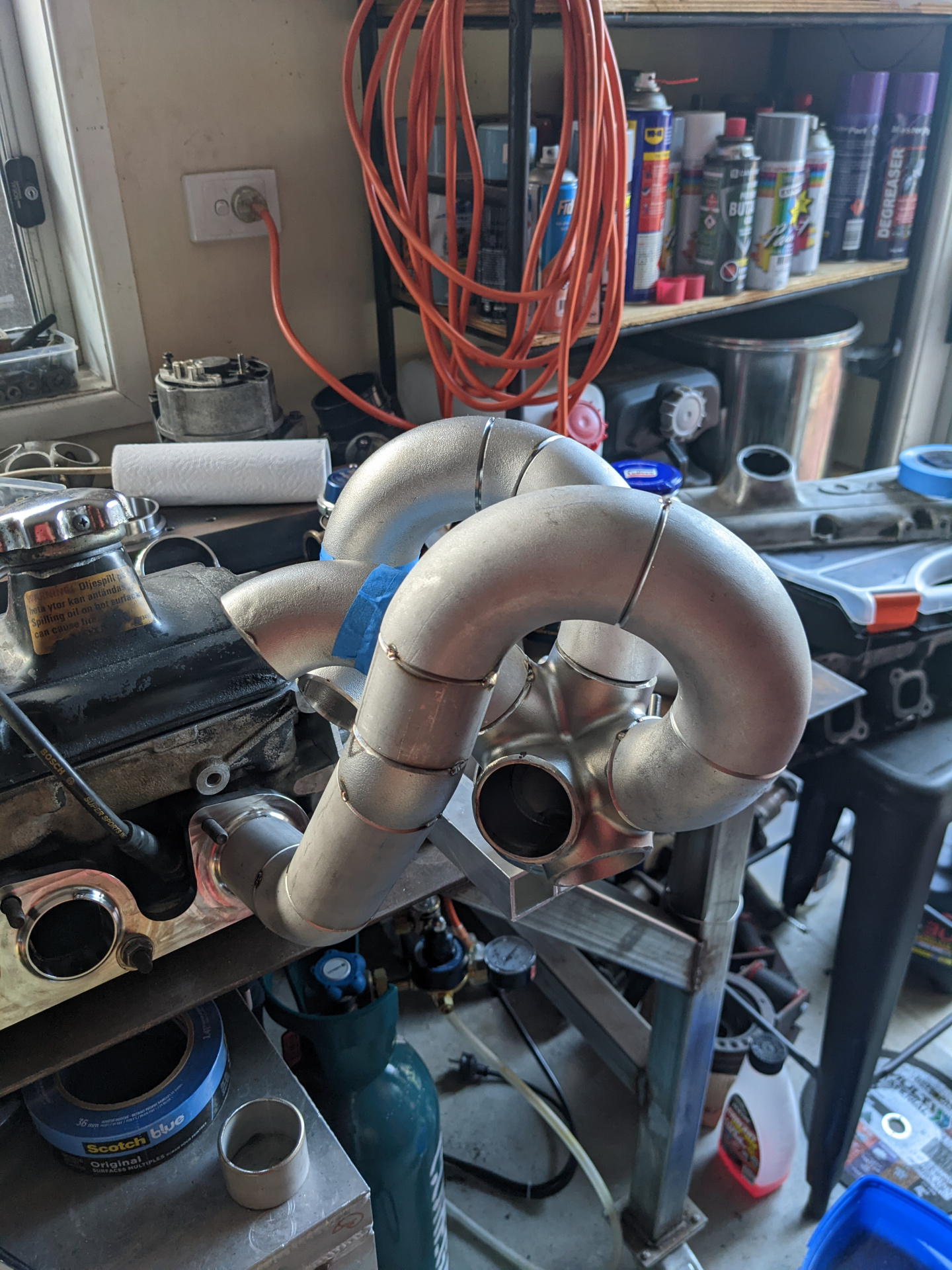
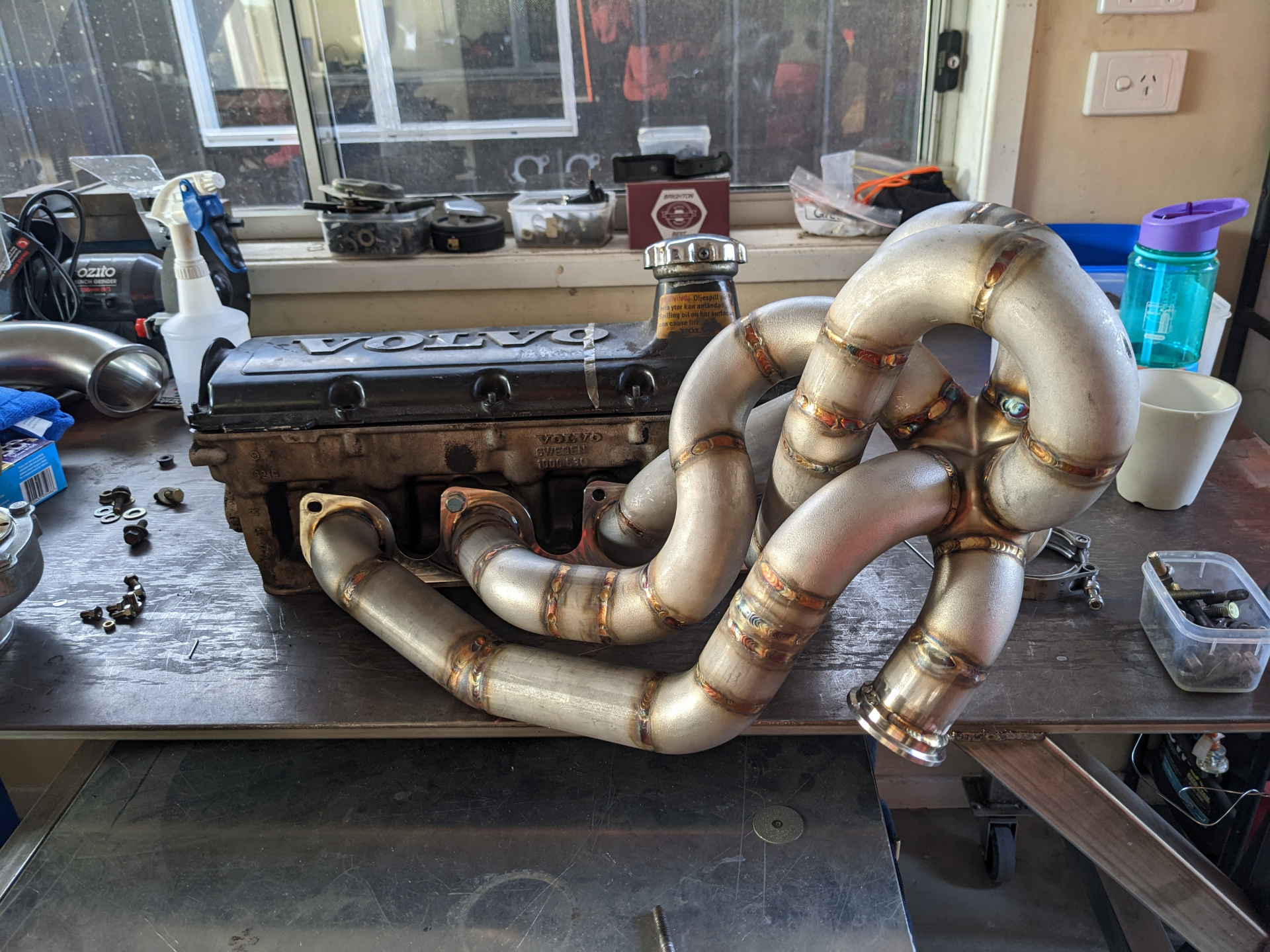
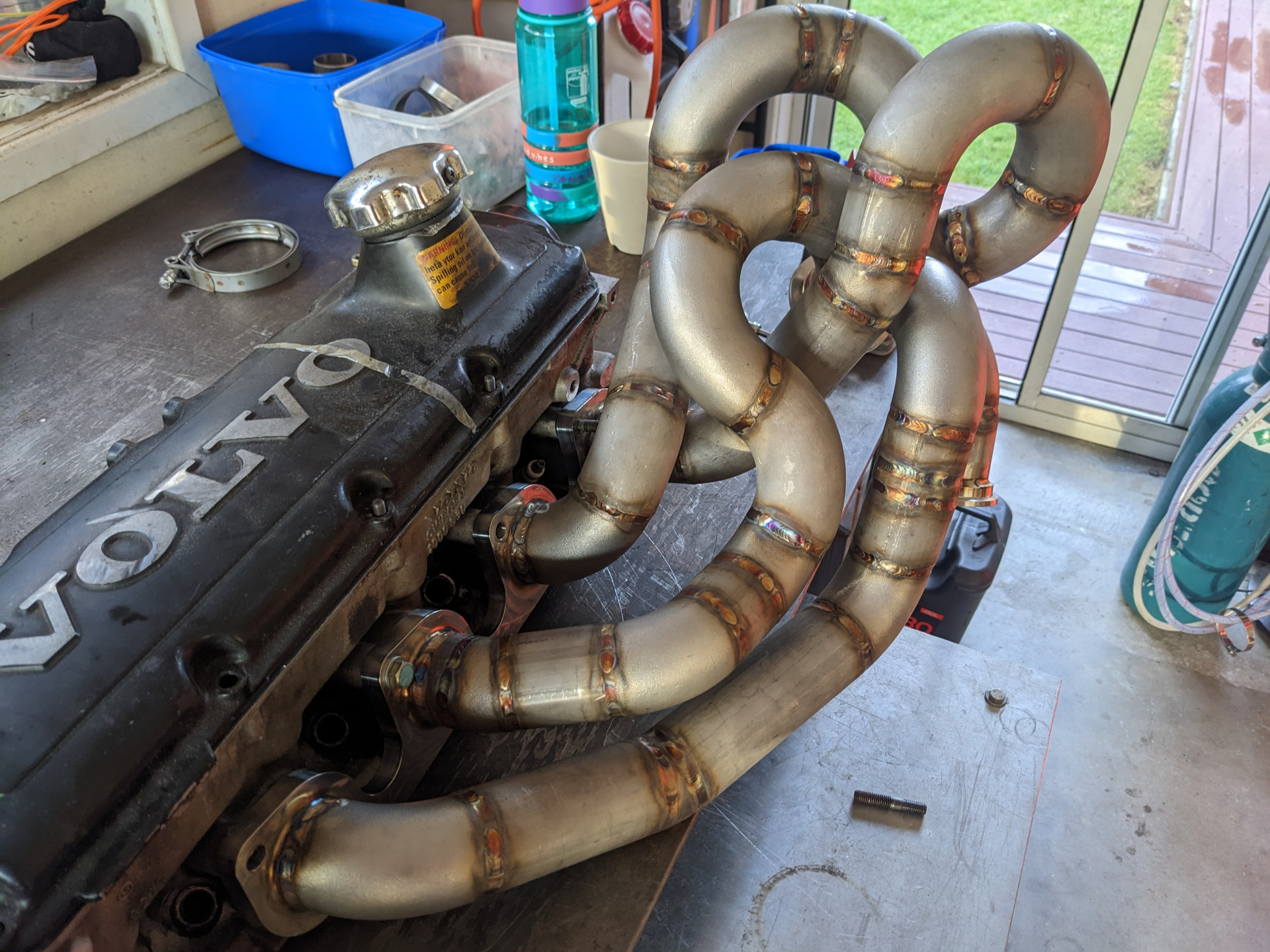
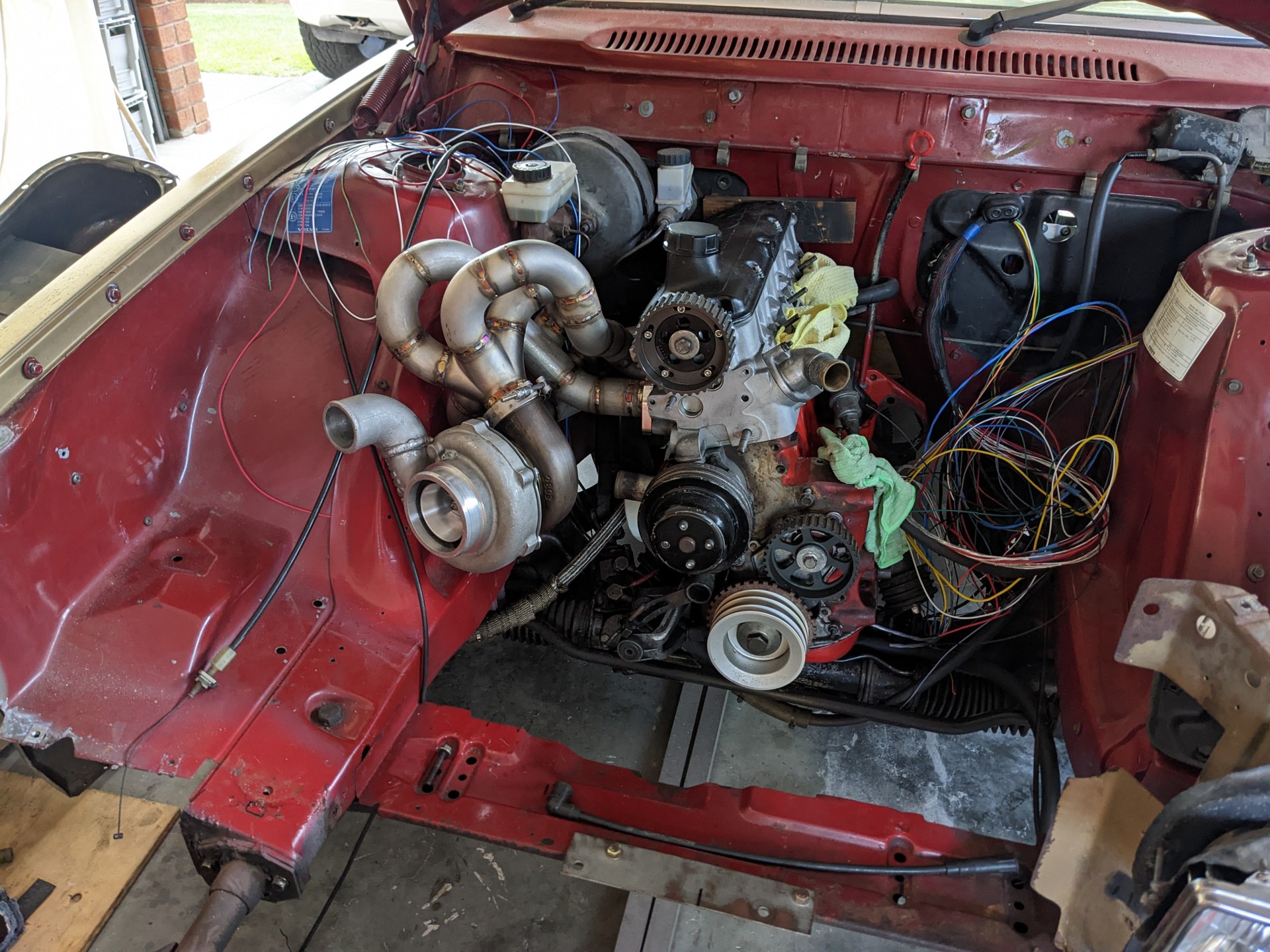
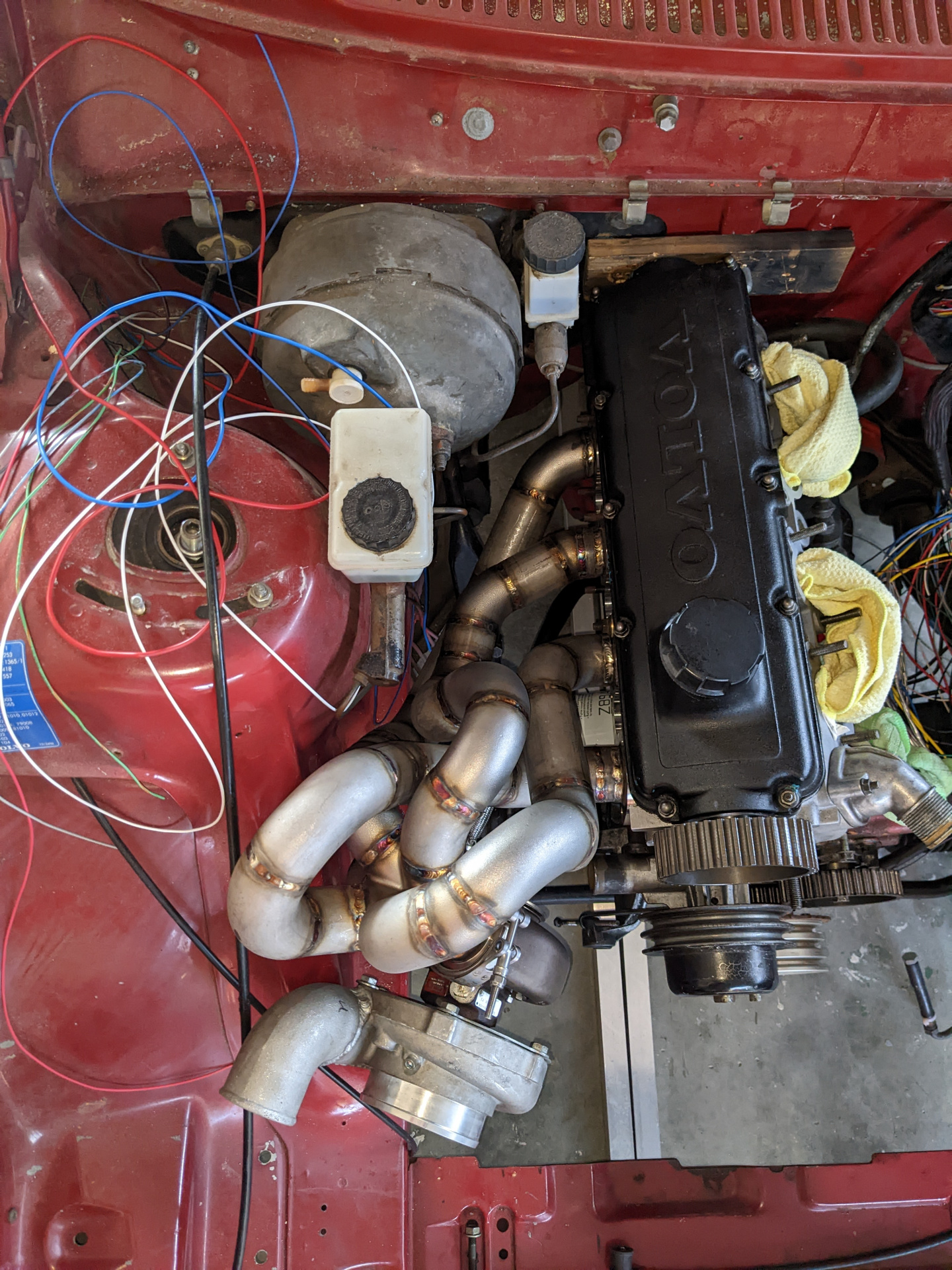
After all that work I really have no idea what to expect from it. It looks cool sitting there though I have no idea if its feasible long term. For a start some welds aren't great as it's my first time doing this kind of thing. Other issues are...
It is sitting out there a fair bit, there's a lot of leverage there. I'm going to have to brace it with a rod/heim joint thing.
Will have to weld a 90* bend onto the water pump inlet to get it away from the turbine housing.
I don't believe there's enough of a gradient in the oil return for the stock return location on the block. I've seen Kenny Howard with his gold car drill and tap in the centre of the block which would fix the issue. I've even contacted him asking about it and his response was there is no problem with it.
It's fairly close to the strut tower, I think the solid mount brace from yoshifab or making my own would keep it from making sweet love to the strut tower.
It's very close to the master cylinder. I can make a heat shield to fit between it all and wrap the manifold, but I don't know if that would be enough to tame the heat. Otherwise changing the booster and/or master cylinder for something more compact would fix it.
The v band flange for both turbo and wastegate warped so will have to cut it off and try again. Spewing about this because I have spent WEEEKS on this thing and just want it finished already.
On the other side of things there's plenty of room for a downpipe. Totally worth it.