- Edited
I'm hoping that someone can help me understand the science behind this problem:
I currently have a Yoshifab crankcase vent plate. The left fitting is the oil drain and the right fitting is the PCV port.
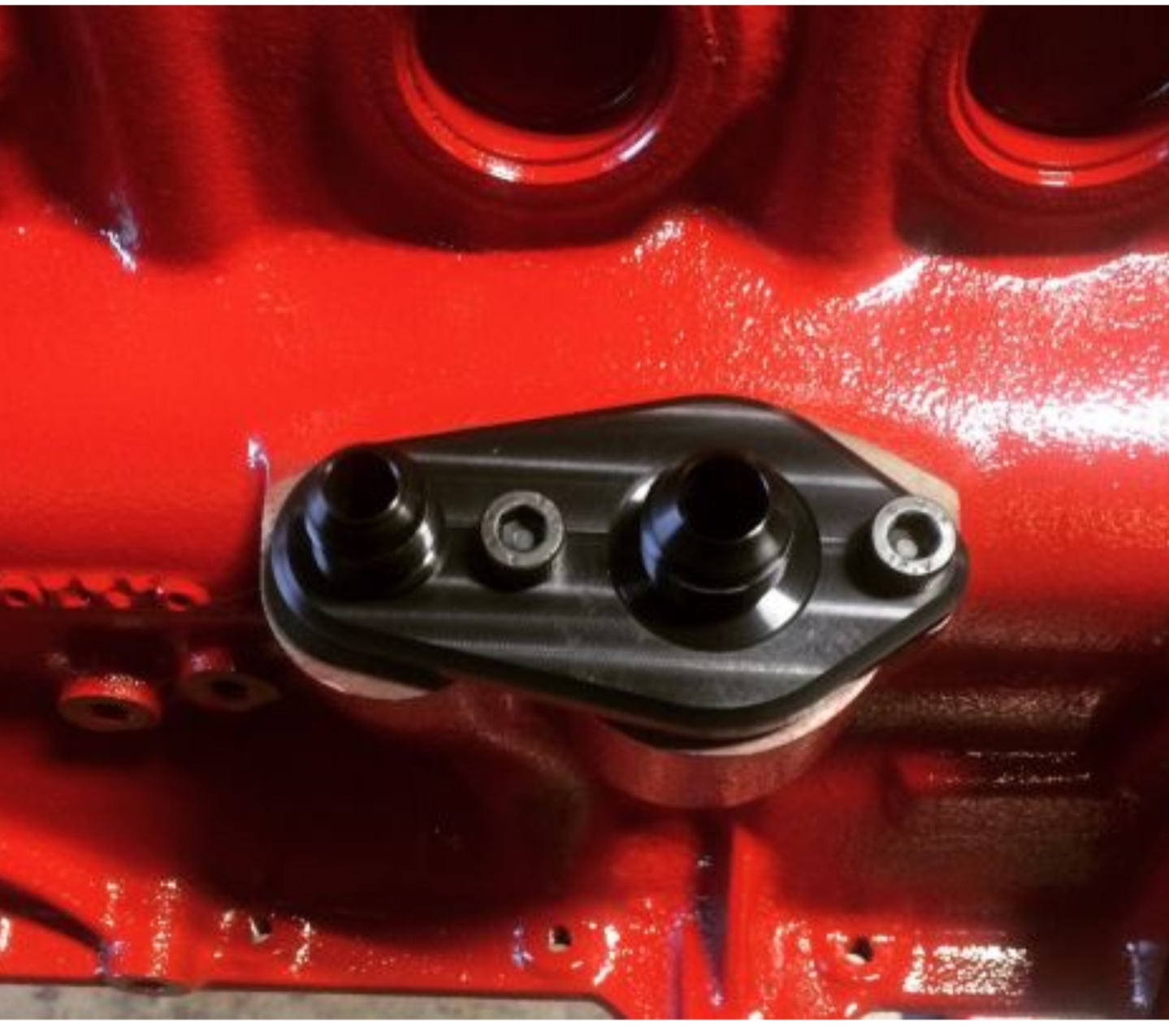
I have my catch can set up like this to drain back to the sump. It also has the oil filler cap vented into it.
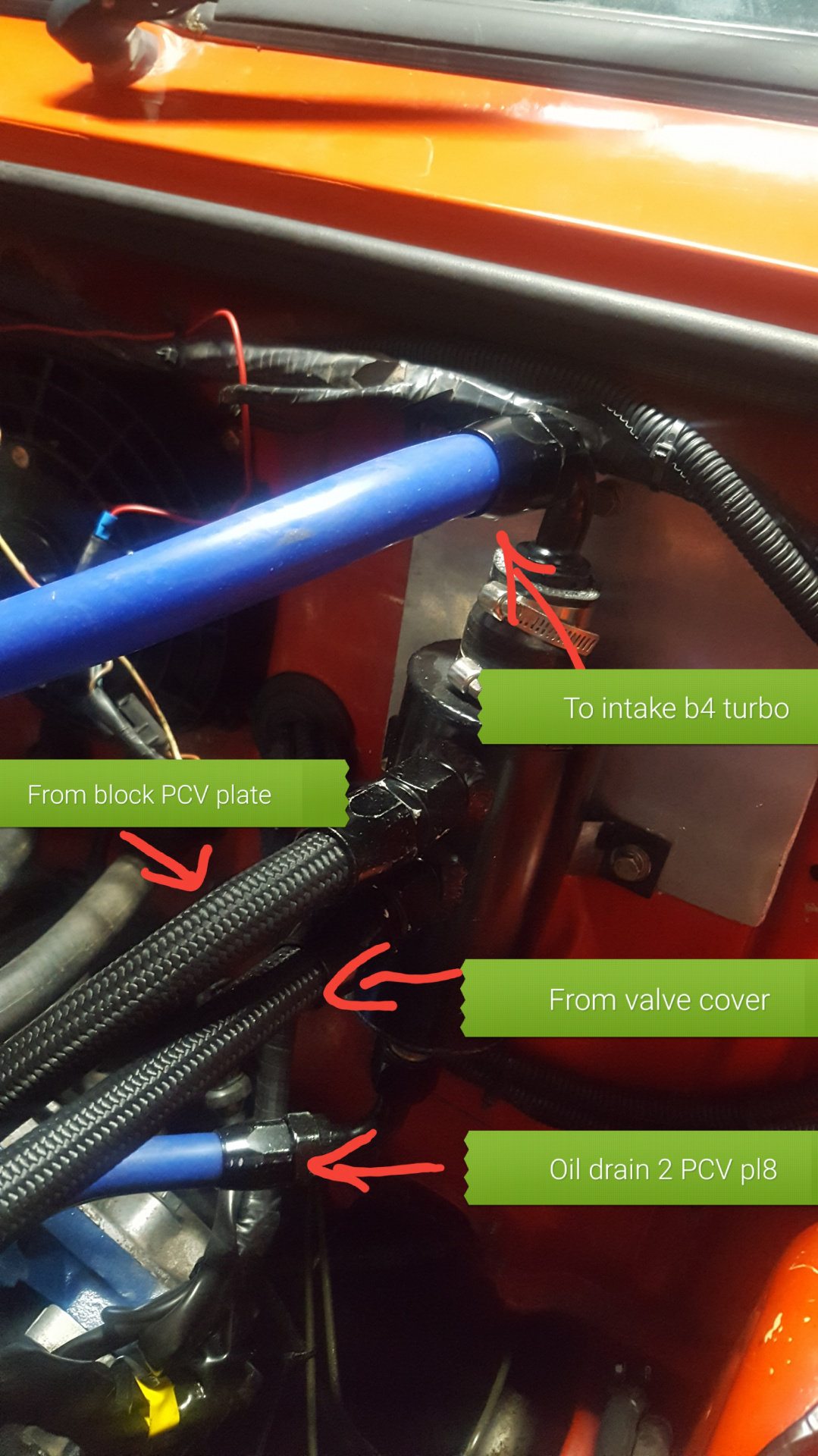
This setup works fine but I'm sick of oil entering the intake before the turbo, so in an attempt to reduce it, I installed another catch can that I had around. I just took the hose going to the intake before the turbo and re-routed it to the catch can first.
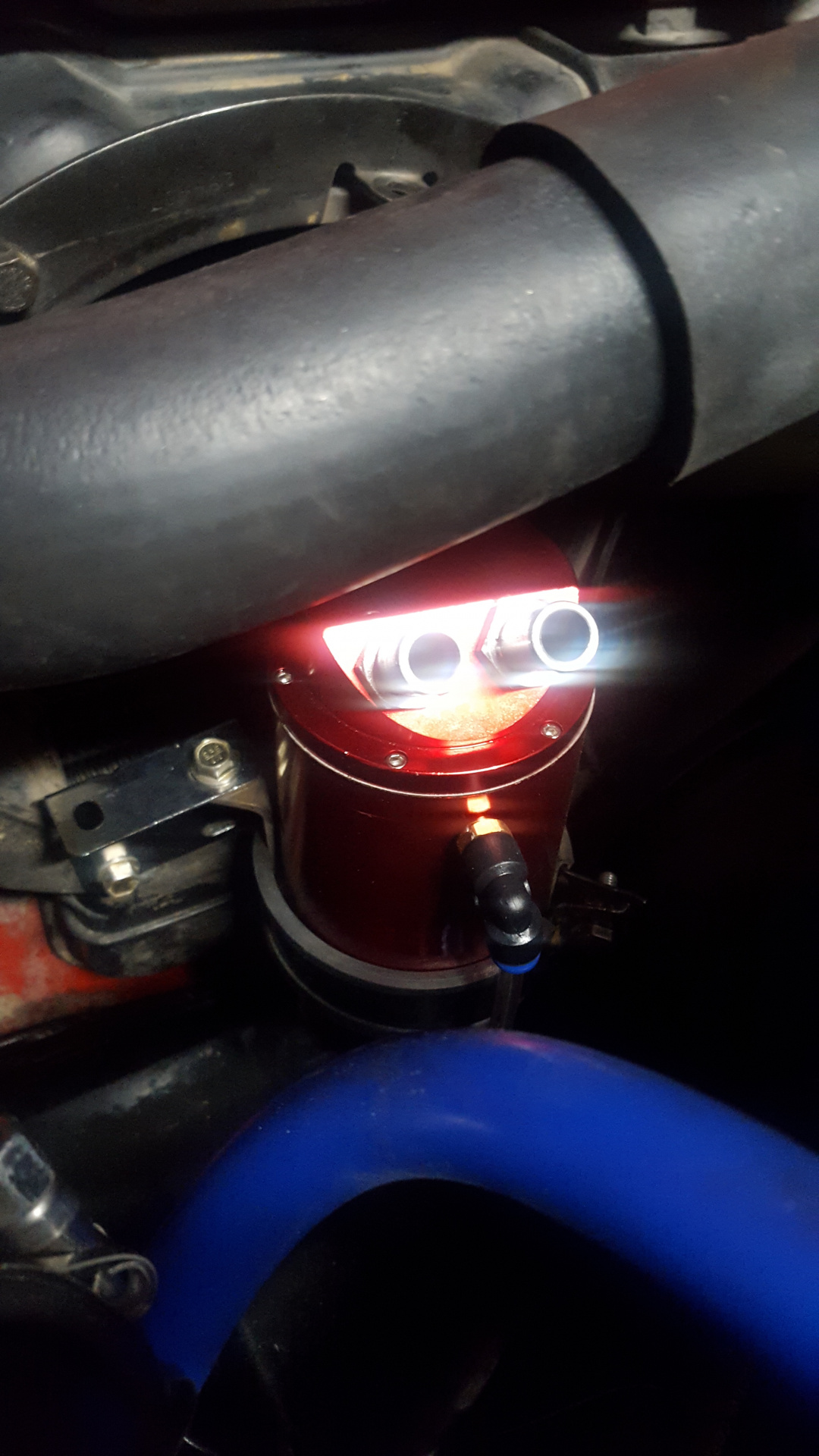
It's a simple catch can. No baffles, just an open can on the inside. But when I connect it inline to the PCV hose going to the intake manifold, it acts like a plug and I end up getting crazy amounts of crankcase pressure. To the point where the valve cover and oil cap leak profusely and I get smoke out of the exhaust after a short drive.
I fitted the old PCV/oil separator box and testes if that did the same thing and it does. I put one way valves inline with the hose going to and coming from the catch can and it still did the same thing.
I don't understand why this would cause extreme crankcase pressure?