Like many of us here, progress is limited by a number of competing priorities that sap our time, energy, finances and sanity.
When I moved the car from WA I had to put a few things on in a hurry, like guards and doors. These have irked me for some time and I've finally put the effort into rectifying these issues. A closer check of some other things like the rustproofing identified some other issues that require attention before it hits the inspection, sometime in the future.
The front guard was put on with some 'really good' adhesive sealant which I now realise was not 'really good' for removal and relocation of the guard. The original sealant was a mastic that never really hardened. For those of us who've pulled the guards off these cars, the mastic is usually still very compliant. Not Tempro Seam Sealer. Luckily I only used this junk on one guard because it is a PITA to get things apart, even taking some of the paint with it.
The guard was finally removed, as was the front door. This allowed me to tidy up some areas of remnant adhesive.
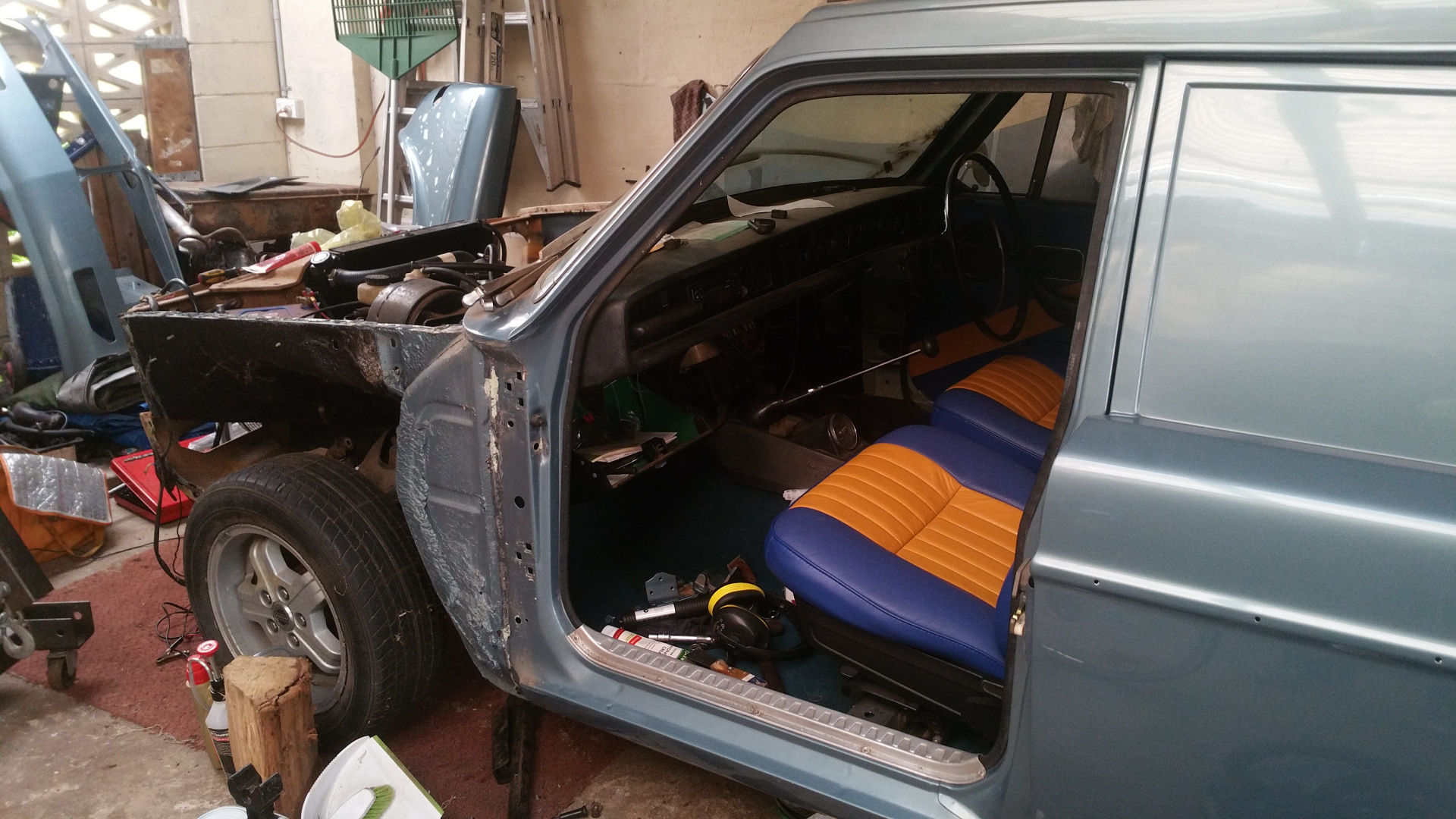
Removing the guard allows access to the seam areas around the inner guard that always accumulate dirt and rust. I scraped these areas back, painted and then brushed on a nice thick layer of sound deadener. Looking at the floor I found areas just behind the front wheel (rock strike zone), along the sill seam and some spots where the floor plates meet. These will progressively get attention as I move from the front of the car to the back.
Fitting and aligning the front door with one person takes ages, but eventually you get there. The results are rewarding when you can finally get things lined up and feel that wholesome thud on closure. The front door on and aligned, I had a quick look at the front seatbelt only to find:
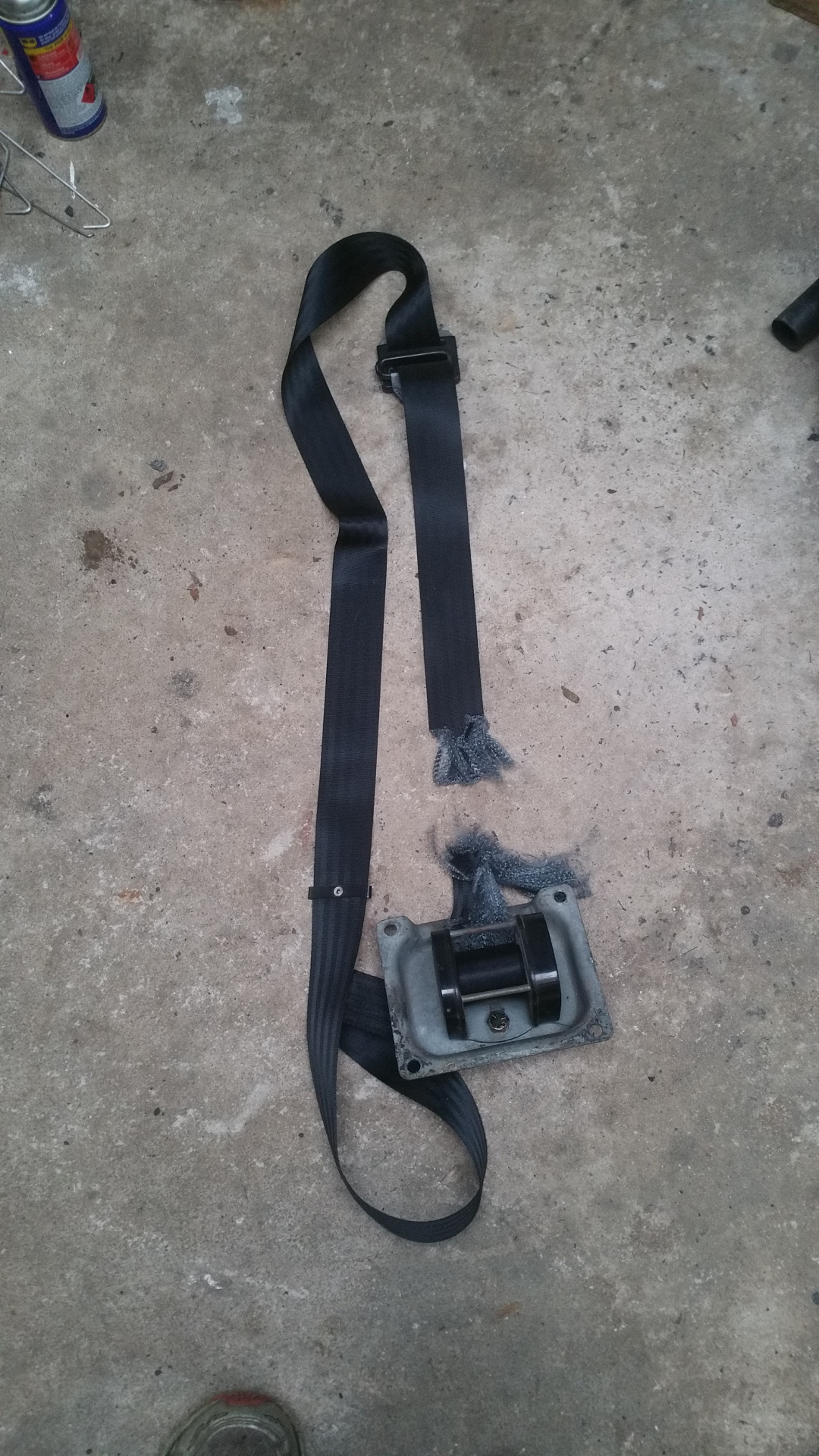
RATS! I somehow managed to get a rat nesting in the car a couple of years ago. Damn thing thought that the 'never used' seatbelt looked like a tasty treat. Now I have to find an aircraft upholsterer to get new webbing installed and certified.
Disappointment aside, I moved onto the alignment of the back door. This van has never had back doors that closed to Volvo standards. After a lot of realignment again and again and again I've settled on an alignment that is as close as I can get it right now. I may have another go at once I've managed to get few more things completed. I'll take another photo soon (pending).